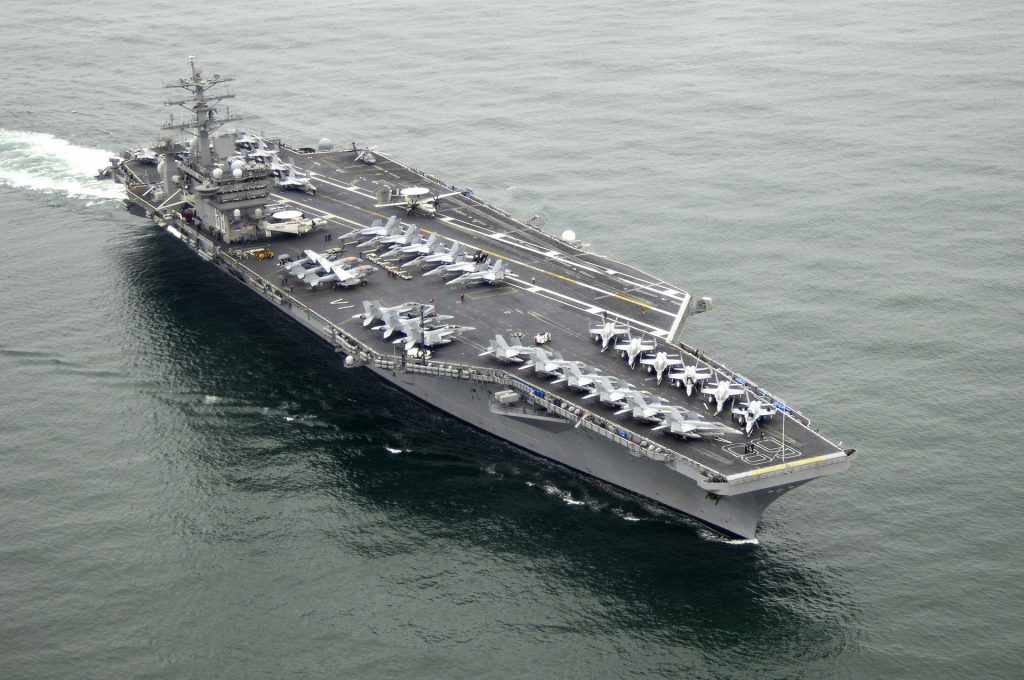
Long and his colleagues at ArcelorMittal Coatesville make high-grade steel used by the military.
Navy veteran Vonie Long knows how important steel is to America’s national defense — in more ways than one.
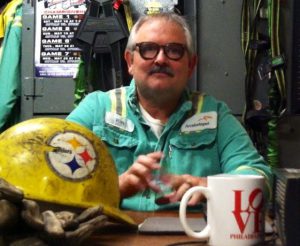
Long served aboard the USS Nimitz aircraft carrier during his time in the Navy, which included deployments in the Western Pacific and Mediterranean Sea. The Nimitz is one of the largest warships in the world, weighing more than 101,000 tons.
The majority of the top-grade steel plate and alloy made for the ship came from the former Lukens Steel Company in Coatesville, Pa. After Long was discharged from the Navy in 1990, he found his way to Lukens Steel.
A fourth-generation steelworker, Long was reluctant to pursue the factory life at first, but the opportunity to produce the highest grade steel and alloy for the military seemed like more than just a job. Long had counted on the mighty Nimitz to protect him at sea, and now he had the chance to be a part of building America’s superior naval fleet.
“Myself, and the other veterans here, are proud, especially the military armory part of our business. It’s like a testament of what we’ve put out in Coatesville,” Long said. “We had representatives come out here in December and talk about how the next three submarines will be built with the majority of our plate. They can honestly get this product from other producers, but they do not get the quality that they get from Coatesville. They cannot find the quality from other producers, and we take a lot of pride in that.”
At the age of 52, Long will soon be celebrating his 24th year of work at what is now the ArcelorMittal Coatesville steel mill. ArcelorMittal has continued the tradition of making essential military-strength products that dates to the opening of the Lukens Steel Company in 1810.
And Long is grateful to be part of it all. Long is an electrician who does preventive maintenance on the mill’s overhead cranes. He also serves as president of United Steelworkers Local 1165, which has 13 units and approximately 1,200 members.
“We are the most important mill to the military. We do a high percentage of the military alloy, so I think it is pretty important to our national defense.” Steelworker Vonie Long
In addition to being America’s No. 1 supplier of military-strength plate and alloy for ships and submarines, ArcelorMittal Coatesville also supplies life-saving products for the Army, including the Abrams battle tank armor, which is comprised of a sophisticated composite metal.
“Military orders are a high percentage of our work, and when it’s needed, it’s made a priority,” Long said. “In the stages of the Iraq War, we went from taking care of all kinds of orders from the military, whether it was melting, rolling, or finishing. Scrap metal comes into the plant and we have the electric arc furnace to make plates and slabs.
“A lot of the maintenance crew here are military veterans and we do take a lot of interest when we see military equipment, whether it by Navy or Army,” Long added. “It piques our interest when we see our product. We’re always asking, ‘where is this going?’ and they might say ‘that’s Army armor or army alloy.’ Just a few weeks ago we got to see the USS Enterprise product.”
Long is referring to melted scrap from the decommissioned, nuclear-powered USS Enterprise aircraft carrier, which will be used in the next generation Enterprise that is currently under construction. Some of the melted plates at the Coatesville mill will be the same steel used in the previous USS Enterprise.
“We’ve done that with the World Trade Center Towers,” Long said. “That was originally our plate, and they took scrap from the World Trade Center after the tragedy and we recycled some of it and made new plate, which is now in the new World Trade Center One.”
Those horrifying photographs of the remains of the World Trade Center Twin Towers after the Sept. 11 terrorist attack show approximately 20 support columns that looked like upright forks. They were known as “trees,” and absorbed the weight of 110 floors above them.
The strength and quality of the steel “trees” became a symbol of America’s resiliency following the Sept. 11 attack, and those steel columns were manufactured at the Coatesville plant in 1968.
Despite the Coatesville plant’s importance to national defense, the amount of work orders at ArcelorMittal Coatesville has decreased in recent years. There are even worries that America’s military will suffer if the mill slowed production or idled.
But with President Trump’s executive order of 25 percent tariffs on foreign steel, workers at the Coatesville facility are buoyed by the prospect of increasing production orders.
“The tariffs are going to benefit us here at Coatesville,” Long said. “Historically, our fight has been on this-product-and-that-product, but by maybe the way the president tackled it with a blanket tariff, well, from my perspective, that’s a big change. It’s better than having the steel come in from Indonesia or somewhere.”
Long’s coworkers also are playing attention.
“Some were not necessarily supporters of the president, but they now finally have someone in the White House who is speaking their language,” Long said. “We are the most important mill to the military. We do a high percentage of the military alloy, so I think it is pretty important to our national defense.”
And a thriving ArcelorMittal Coatesville mill is also important to Long’s middle-class lifestyle. Along with his wife, he has been able to raise four daughters and purchase a home in Mohnton, Pa. which is about 45 miles west of Coatesville. He has a pension fund and health care coverage for his family.
“I wouldn’t be doing this and having a 45-minute commute and invested over 20 years now if I didn’t think it was good work,” Long said. “I work on trade issues with the USW and other family-type issues, because I want this work to be here for my grandchildren. I’m a fourth-generation steelworker and I want this work to be here for my grandkids and their grandkids.”