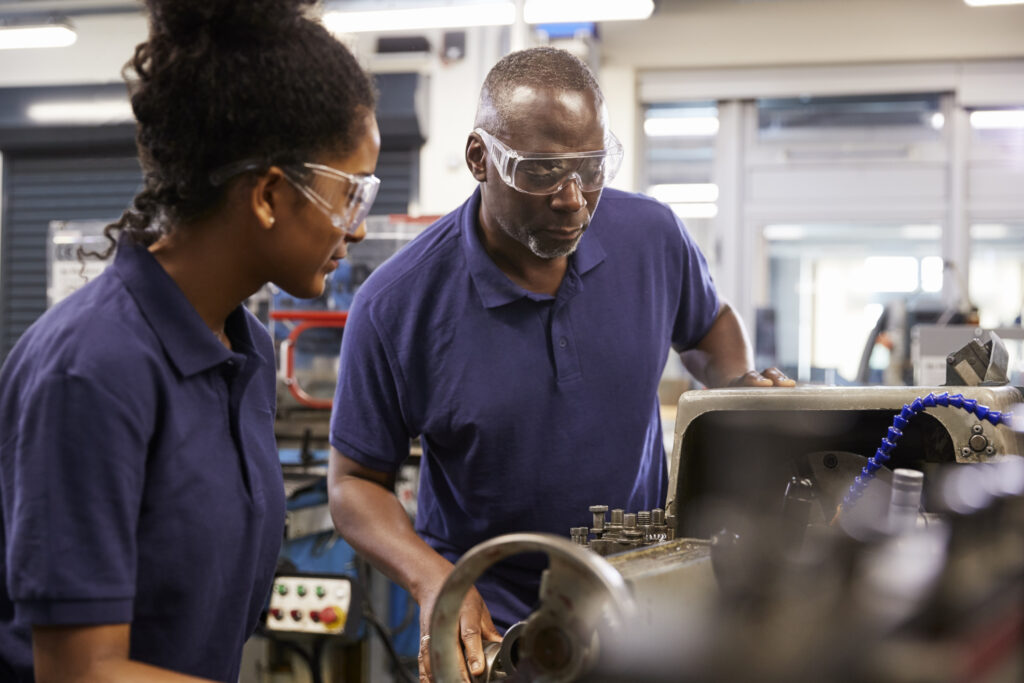
Companies often complain about the “skills gap.” But the public and private sector aren’t doing enough to train workers and line them up with good-paying jobs.
Editor’s note: This is the ninth entry in our 10-part series examining the policies and priorities that President-elect Joe Biden should focus on as he looks to lead America out of the COVID-19 pandemic and rebuild the American economy.
President-elect Joe Biden fashions himself as a fighter for the middle class. He’ll need to put all of those credentials to work in order to reshape the way in which we build pathways to the middle class for more Americans. If we want a sustainable future for manufacturing in the U.S., it’s essential that we reimagine skills and training opportunities.
While many employers—including manufacturers—loudly complain that they can’t find skilled workers to fill positions, many labor market data points indicate that isn’t the most significant obstacle. For instance, there are still 600,000 factory workers unemployed since the onset of the pandemic.
In my conversations with factory owners around the nation, one thing seems true: Employers who offer superior pay, benefits, and opportunities for skills development and promotions tend to find qualified applicants more effectively than employers who do not. When employers heed the words of Jerry Maguire character Rod Tidwell, “SHOW ME THE MONEY,” they get better results.
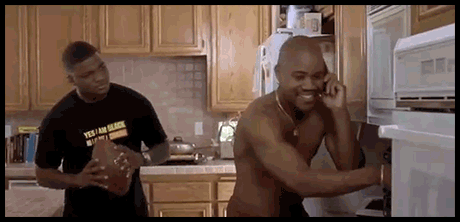
Still, some business associations loudly proclaim a “skills gap” as the primary cause for concern. I’d suggest that other gaps present far greater obstacles.
First, there is an opportunity gap. Our public and private sectors simply don’t invest enough in training workers. Despite the presence of some top-notch local training programs and exemplary employers, overall, we are global laggards.
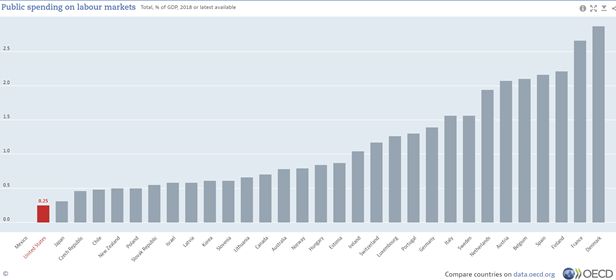
Those opportunities that do exist are inequitably distributed. The National Skills Coalition, whose board I am honored to chair, has shown that communities of color historically have had relatively less access to training programs and community colleges than whites.
Second, there is an expectations gap. Factories once had a pipeline to new talent straight out of high school shop class. But most manufacturing jobs today require more than just a high school degree, and career and technical education has received short shrift in secondary education. Not enough employers offer to pay for skills and training programs beyond high school. Community college and technical education, while less expensive than a four-year college degree, may still be out of reach for students fresh out of high school or for adults seeking new careers while also managing child care, housing expenses, and other responsibilities.
Third, there is a demographic gap compounding all of this. Retiring Baby Boomers made up the majority of the factory workforce for a long time. Meanwhile, for the better part of a decade, manufacturers weren’t hiring scores of new workers. Instead, they were closing down, shipping jobs overseas, or laying off workers in the face of surging imports from China. That meant the career and training programs available to new labor market entrants were focused on other jobs. The replacement rate for manufacturing workers has suffered as a result. Realigning the system is still a work in progress, as many younger students are urged into a four-year college or a career outside of manufacturing.
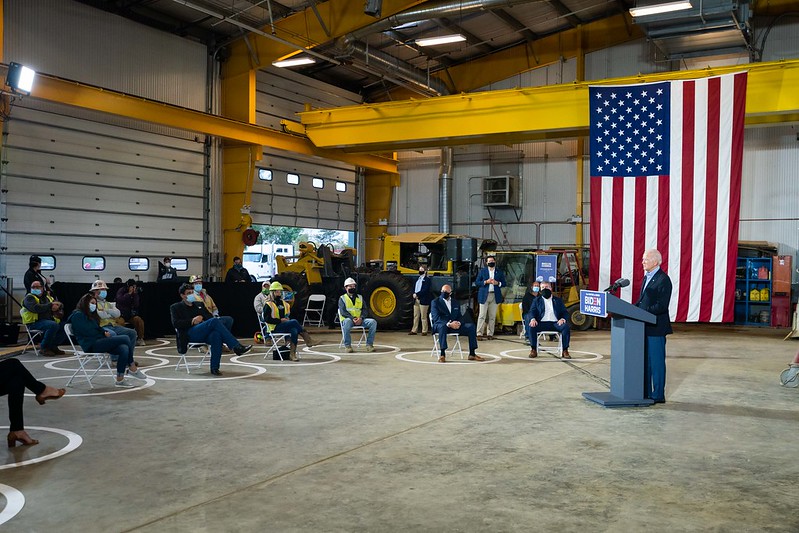
President-elect Biden’s plan for career and technical education recognizes these challenges and offers up some solutions. For example, students (and returning adults) would receive two-years of free community college or high-quality career and technical education, with more built-in support services to increase the chances for completion. The Biden plan also invests more in apprenticeships and sectoral partnerships. Both are field-tested solutions that would benefit from scale and resources.
In addition, the National Skills Coalition released an ambitious framework for an inclusive economic recovery. The incoming administration would be wise to adopt these wide-ranging recommendations as it constructs its “Build Back Better” agenda.
One final thought: I’m a trade hawk who strongly believes that getting tariffs and other economic levers right is essential for manufacturing’s future in America. None of that will matter, however, if we don’t invest in our workers to ensure that we are competitive and sustainable. This isn’t an either/or choice. We must do both.
Listen to Scott Paul talk about this blog on The Manufacturing Report podcast.