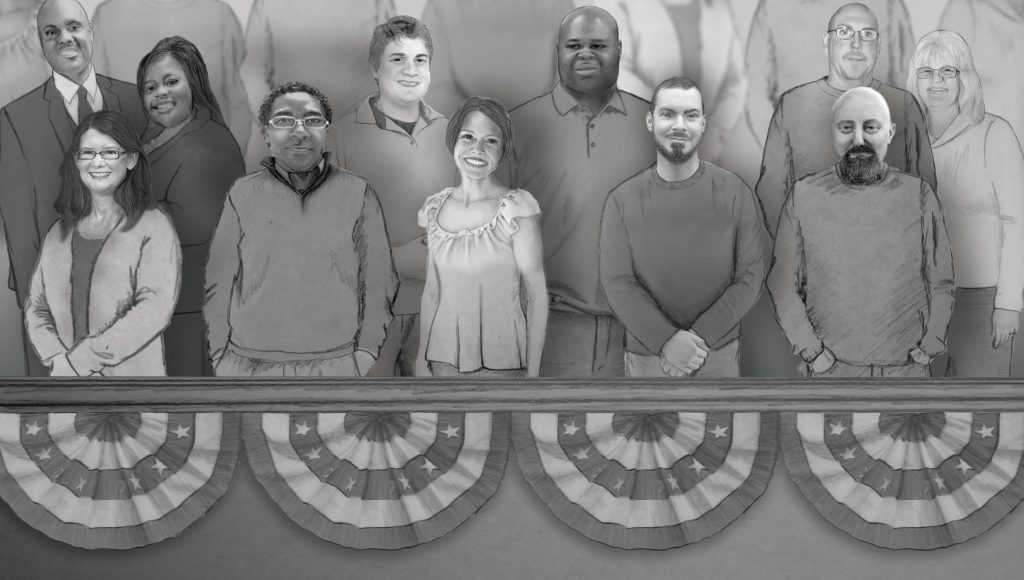
We asked Americans in manufacturing about the State of the Union. Here’s what they said.
It's almost time for one of Washington, D.C.'s grandest political events: The president's State of the Union address to Congress, where the commander in chief lays out upcoming policy plans and highlights political achievements. And it's a decades-old tradition that the White House invites a list of VIPs to sit alongside the first lady for a front-row seat to the pomp and pageantry.
These VIPs are often reflective of political goals the administration du jour is pursuing, and an invitation to the address is considered a high honor. That's why the Alliance for American Manufacturing decided to create a viewing box of our own. We wanted to know: What's the state of the union, from the eyes of everyday Americans working in the manufacturing sector? To find out, we spoke to Matt Snodgrass, David Ramirez, Melinda Allen, Kyle Worzala, Gayle Goodrich, Luke Diserio, Mike and Dorothy Miller, Jessica Graves, and Durwin "Oodie" Royal. Here are their stories.
Matt Snodgrass: Worried About the Next Generation
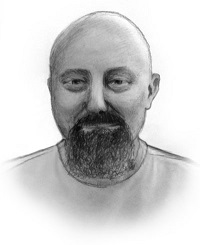
In the 18 years that Matt Snodgrass has worked at the Mondi North America packaging facility in West Virginia, he’s seen a lot of change.
In owners, that is.
The factory — which manufactures a range of paper bags (think everything from sugar to dog food to fertilizer) — has switched hands eight times since Matt first started. And while he continues to enjoy his job, Matt is concerned about what the future might hold, especially since the bulk of Mondi’s business is based in Europe and Asia.
“I’m afraid that they’re going to take our business here and move it over there,” he says.
Although he’s been at the facility for nearly two decades, Matt knows what it’s like to be out of work, as he worked 11 different jobs after leaving the military in 1989. When he landed in 1997 at his current factory, things changed for him and his family.
“It was a lot of stability, a lot of stability,” he recalls. “It was nice to know that I had at least — at least — a 40-hour week. I probably averaged 50 to maybe even 55 hours a week. I felt pretty stable… you have your bad days, but you have more good than bad.”
But now there are signs of trouble, he says. The factory’s sister plant in Ohio closed in December. Meanwhile, the paper bag industry is facing stiff competition from plastic containers.
It was nice to know that I had at least — at least — a 40-hour week. Matt Snodgrass
Matt also is concerned about the next generation. His 24-year-old son just got out of the Air Force and hasn’t been able to find a steady job. To make ends meet, he is working for minimum wage as security guard. “There’s a lot of youth out there that want to work, and can’t,” he says.
Matt hopes that President Obama will remember workers like him and his son and “take care of your own.”
“Take care of what’s here. Don’t worry about everybody else so much,” Matt adds. “We have a lot of smart people in this country, put them to work.”
-Elizabeth Brotherton-Bunch
David Ramirez: Securing His Future
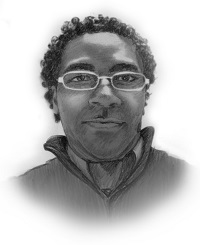
Working as a jack-of-all-trades technician for the Holland Company by day and attending courses at Ivy Tech Community College by night, 39-year-old East Chicago, Ind. resident David Ramirez is striving to improve his future – not only for himself, but for his three children as well.
David attends night school three times a week. He’s enrolled in the Steelworker for the Future program, two and a half years of coursework in which credits earned apply toward an associate’s degree in Applied Sciences.
“I’m hoping to be employed as an industrial electrical maintenance technician after receiving my degree from Ivy Tech,” David says. “I can take this knowledge and work anywhere in the world to help me secure a stable future for me and my family.”
With a first-year curriculum consisting of Applied Technical Mathematics, Key Principles of Advanced Manufacturing, Technology of Advanced Manufacturing, and Basic Electricity, David expects to use the knowledge he gains through school, combined with hands-on experience from work in his future career.
“This first semester has been a big struggle for me,” he says. “Everything is new. I’ve only been raising my children for the past year and a half, so I was used to being a single man. It’s a constant juggle between taking care of my children, working, and attending classes.”
To maintain this lifestyle, David wakes up at 4 am every day to get himself going. He then brings his children to daycare, proceeds to work, and caps his day off in the classroom.
I can take this knowledge and work anywhere in the world to help me secure a stable future for me and my family. David Ramirez
Despite the early mornings, long days, and late nights, David is optimistic for his future. He’s fought through all the curveballs life has thrown at him so far, and says he’s headed in the right direction.
“I’ve gotten over the first hurdle, and so long as I can stay balanced I see a bright future ahead,” David says.
-Ryan Lombardozzi
Melinda Allen: “First things come first.”
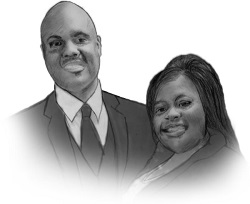
Melinda Allen is 45 years old. She’s married with three kids – one of whom is in his first year at Middle Tennessee State University – and has worked on the HVAC unit production line for Carrier Corporation in Collierville, Tenn., for more than 11 years. She’s experienced three work stoppages in that time.
The latest one came just before the holidays.
“I was laid off the second week of December, and I’m laid off until March,” she says. “I don’t know the exact date I’ll return to work; the only thing (the company) said is the month of March.”
Her husband, Anthony, is also a Carrier employee. His job has been idled, too.
“Just so happens, thank the Lord, that he’s got a part-time job at the post office,” says Melinda. “So we’ve gone from a dual income to now just a part-time income and my unemployment. Can you imagine?”
This December was a little difficult, but Melinda says her family is supportive.
“Me and my husband, we always sit down with our kids when a hardship has hit us. We explain, ‘mommy and daddy will not be able to do this this year, but we guarantee that when we can do something, we’ll do it.’ Because we explain to them, ‘first things come first,'” she says.
We’ve gone from a dual income to now just a part-time income and my unemployment. Can you imagine? Melinda Allen
Melinda plans to seek out temporary employment to bridge until Carrier picks her back up in March. But the constant job insecurity is an unwelcome presence in the Allen household.
“I love my job,” Melinda says, “but I can’t take getting laid off. You fall behind on your bills, end up in hardship, and when you return back to work, you’re trying to catch up. It’s very hard.
“I pray we aren’t laid off again, because it’s hard out here. We need to work. That’s how we pay our bills, it’s how we eat, and do the things we need to do in life. We depend on our jobs; that’s why I go every day.”
-Matthew McMullan
Kyle Worzala: Everything’s Looking Good
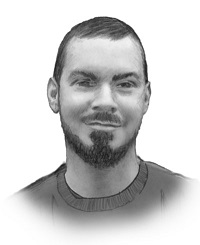
Kyle Worzala has been welding since he was five. He developed a passion for it and has been on the job since he was 18 — five years.
“Getting into welding at an early age was very beneficial to me,” Kyle says. “I was able to see that it was cool and something I could make money doing. Now, when I walk into work, it’s not like I’m working, because I enjoy my job.”
The lifelong welder found a permanent position at P&H Mining, a Milwaukee subsidiary of Joy Global, Inc. that builds and supports drilling and material handling machinery for surface mining. Unfortunately, the position wouldn’t prove steady.
In 2013, there was a big layoff, Kyle says. He describes getting laid off in one word: scary.
“You don’t know when you’re coming back,” he says. “You have to go and find work. And it feels like entrapment because you know how the job market is. You know you need to take this job, but the wage may not be competitive.”
When I walk into work, it’s not like I’m working, because I enjoy my job. Kyle Worzala
Kyle didn’t end up getting another job during his layoff. Instead, he spent his time reading and studying to learn about welding inspection. “So I have a Plan B next time,” he says. He spent time as a volunteer welding instructor at a local high school.
But for now, he’s still working with Plan A. Kyle was called back to work in February 2014. Slowly but surely everyone has come back to work, he says. And P&H Mining is even looking to hire more, due to a shortage in welders.
“Everything’s been looking good for us,” Kyle says.
– Taylor Garland
Gayle Goodrich: A New Job, But Continued Uncertainty
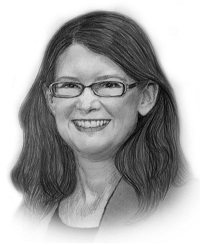
As part of her duties as the AFL-CIO community services liaison for the United Way of Allen County, Ind., Gayle Goodrich supports local workers who are impacted by layoffs or facility closings.
Gayle speaks from experience. She was among the 1,400 workers at Navistar in Fort Wayne who were laid off in fall 2012. While the 45-year-old landed on her feet, things remain tough for many in Fort Wayne, where some former Navistar employees are still struggling to find work.
And that continued uncertainty is now impacting Gayle's current position.
“The economy has been hard on us nonprofits because the need has gone up, but it’s hard to raise money because a lot of people lost their jobs in the recession,” Gayle says. “I’m sure that a lot of folks, even if they’re working again, they might have used their savings or their 401K, so they’re trying to rebuild that.”
After Gayle was laid off in December 2012, she didn’t get a lot of interviews, and the job offers she received paid far less than her former position at Navistar. It took seven months to find her current job, and while she took a pay cut, it was one she could live with, she says.
I really hope that we can go back to where we were even 20 years ago. It just seems like working people have not fully recovered from the recession. Gayle Goodrich
But since she had a sociology degree and experience in human resources, Gayle had an edge on many of her former colleagues, most of whom had an engineering or technical background.
Fort Wayne doesn’t have enough technical jobs to support those workers, Gayle says. And she’s concerned that there aren’t enough middle class jobs left anywhere, ones that allow people to do things like buy a house, pay their bills and take care of their families.
“I really hope that we can go back to where we were even 20 years ago,” she says. “It just seems like working people have not fully recovered from the recession.”
In the meantime, Gayle will continue to do what she can to help those going through tough times. “I can come and say, ‘I know what you’re going through,’” she says.
-EBB
Luke Diserio: Continuing the Tradition of American-Made
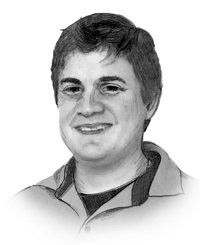
Luke Diserio, CEO of American Muscle Docks (AMD), and a native of Wellsburg, W.Va, is no newcomer to American-made.
This ever-evolving family business began with his grandfather, Paul J. Desiero, who incorporated an American-made metal fabricating and stamping business in 1963. He named his venture Valley Manufacturing.
In 1988, his father, Paul R. Diserio, took over and turned the business toward the fabrication side of manufacturing. In 2012, Valley Manufacturing made the decision to purchase Follansbee Dock Systems and brought both businesses under a new name: American Muscle Docks & Fabrication LLC.
“I’m proud to have the heritage going on and to be able to continue that tradition of being family owned and American-made,” Luke says.
We’ve jumped a huge hurdle in our first year and now have our feet under us. All of the stuff we did early on will finally pay off. Luke Diserio
Originally employing six employees with yearly annual sales averaging $500,000 from 1999 to 2012, AMD in its first year expanded to 22 full and part-time employees and produced over $2 million in sales.
“Business has been looking good and I’m looking forward to what the future has to hold. From what we’ve done in the past three years in terms of marketing, sales, shipping and building has been amazing,” Luke says. “We’ve jumped a huge hurdle in our first year and now have our feet under us. All of the stuff we did early on will finally pay off. All the dominos have fallen right and this year is the year when it all happens.”
Despite having a productive first year, AMD still has concerns for the future, especially with the fluctuating prices of steel and raw materials. “People who build just want the cheapest product, so we don’t want the Chinese or other markets to rip-off and produce a lesser version of what we offer,” Luke says.
If the price of steel increases in the United States, it would not only hurt AMD domestically but globally as well.
“Another concern I see is our ability to take out loans to help our business grow when needed without having to sacrifice anything as well as finding the money needed to reinvest into our company,” Luke says.
-RL
Mike and Dorothy Miller: The Golden Years
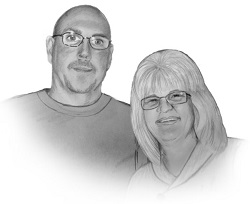
Mike and Dorothy Miller live in Cleveland, where they raised a family on manufacturing salaries. Mike started work in 1972 at a paper mill, and until recently worked as a die maker.
“I’ve worked it all in the paper industry,” Mike says. “When I got out of school, there were factories on every corner, I’m telling you. There were mom-and-pop factories, big factories, there was no problem getting a job anywhere back then.”
Dorothy started work after their son began school. She’s since spent 28 years at a Hugo Boss suit-making factory in the Cleveland area. “I’ve pretty much trained my supervisor on this job,” she says.
But all is not well. Mike was laid off from his last job last spring, as his facility closed after importing more of its paper products from China.
“They would ship cartons back already packed in cases with our company’s name on them,” he says. “All we did was break them down off of the pallets and ship them out to the customers.
“I don’t even know if those customers knew that the product came from China or not. As long as they’re getting the product.”
Mike is 61, has filed for his pensions and continues to draw a salary from work related to his union. He’s more concerned for his wife. Dorothy’s factory will close its doors in April. “She’s 53 years old. Where are you gonna go now, at 53, looking for job, if they close that facility? That’s been kinda her whole life. She knows all the ins and outs of manufacturing high-end clothing.”
I don’t even know if those customers knew that the product came from China or not. As long as they’re getting the product. Mike Miller
Dorothy explains:
“We downsized once before. Hugo Boss decided four years ago that they wanted out. They offered severance packages, but the union fought, and they saved our jobs.
“I wanted to keep working. I needed a job, and I have bills to pay. So they took back a week’s vacation, and I think $3 or $4 an hour I gave back, just to keep my job.
“After all the concessions, there was no sign that they weren’t going to renew the contract. We thought we were just gonna get ready to start negotiating; they asked if I’d like to be on the negotiation committee for the next contract. But I guess that wasn’t in their plans.”
Dorothy plans to look for work, though she’s not sure where she’ll end up.
“They say these are the golden years, but I don’t know if I’m liking them yet,” she says. “I’m looking for my husband to be comfortable, to have insurance on both of us, to have a house. All the things the all-American person wants. I can’t just give up, I have to find something out there.”
Despite it all, Mike and Dorothy remain optimistic. One of their kids started a small business, making and selling training cups for children and the disabled. With some gentle urging from Mike, the product is fully American-made between Pennsylvania and Ohio.
As for the future, Dorothy had this to say: “We’re strong. We’re very motivated. I’ll find another opportunity out there, though right now I’m not sure in which direction I want to go. My husband is very strong and supportive, and so are my children. I can’t buy them the luxury gifts that we once did, but it is what it is.
“Like my grandson, who’s 10, said to me, ‘Grandma, I don’t care if you buy us anything, as long as you’re here with us for Christmas, that’s all that I want.’ That was the best Christmas gift that I got.”
-MM
Jessica Graves: Optimistic About the Future
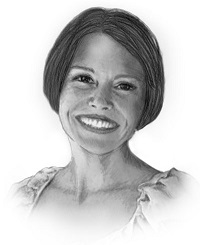
It all started in the kitchen for Jessica Graves.
A self-described “chemistry geek,” Jessica grew up studying plants and working on an organic farm. So when she had trouble finding locally sourced and affordable organic products for her sensitive skin, Jessica decided to make some herself.
That do-it-herself attitude led to Pittsburgh-based Una Biologicals, which is now sold at 48 retail locations nationwide and employs nine people. And Jessica expects the best is yet to come.
“We’re looking into some bigger growth,” she says. “Bigger space, bigger tools, bigger machines… We’re really excited about this next year in terms of growth and moving forward.”
In the next few years, Jessica hopes to open several retail storefronts for Una Biologicals, first regionally and then nationally. She also looking to expand the reach of the skincare line, including to receptive overseas markets.
I think you have to do your part. Jessica Graves
That’s not to say Jessica is naïve about the hurdles that lie ahead. The company is at the tricky phase of growth for a small business, when growth must come at the right pace, she says. Meanwhile, affordable real estate is hard to come by, especially in expensive urban areas.
But Jessica remains optimistic for her Made in America brand, especially in a place like Pittsburgh, which has seen a rise in small businesses and independent shops that is “bringing a lot of creativity and growth” to the city, she says. And Una Biologicals makes sure to walk the walk by sourcing from U.S. suppliers whenever possible.
“I think that is really important,” she says. “I want people to support my small shop. I think you have to do your part.”
-EBB
Durwin “Oodie” Royal: A Worker Turned Advocate
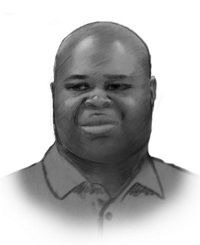
Oodie Royal does what it takes to make a better life for his family and community.
After starting his own janitorial business in Washington State, Oodi moved home to East Texas to raise a family because he knew there was an opportunity to provide for them: A job at U.S. Steel Lone Star Tubular Operations that would afford Oodie and his family a good, middle-class lifestyle.
“The job I have, I can afford to send my kids to college,” he says. “I live in a nice, modest home. I can take vacations every now and again. It pays me enough that I don’t have to worry about going home and if my kids can eat.”
During his 20 years at the plant, Oodie began working in union leadership to advocate for his 1,200 coworkers, a job he takes very seriously. The plant is the heartbeat of four towns in East Texas and, as Oodie tells it, pumps money back into the economy.
The job I have, I can afford to send my kids to college. Durwin "Oodie" Royal
This heartbeat was exposed last year when jobs at U.S. Steel Lone Star were threatened by a surge of imported steel pipe from South Korea. Oodie traveled to Washington, D.C. with fellow steelworkers to urge the government to enforce its trade laws.
“We are the engines that drive the economy,” he told lawmakers and administration officials. “If you allow these jobs to go overseas and cut jobs like ours. No one will be able to buy the things that are imported.”
It was a success. The plant was able to hire 200 to 300 employees over the last year. After a tumultuous year, fluctuating oil prices could threaten jobs in Lone Star.
“I’m cautiously optimistic about the future,” Oodie says.
-TG