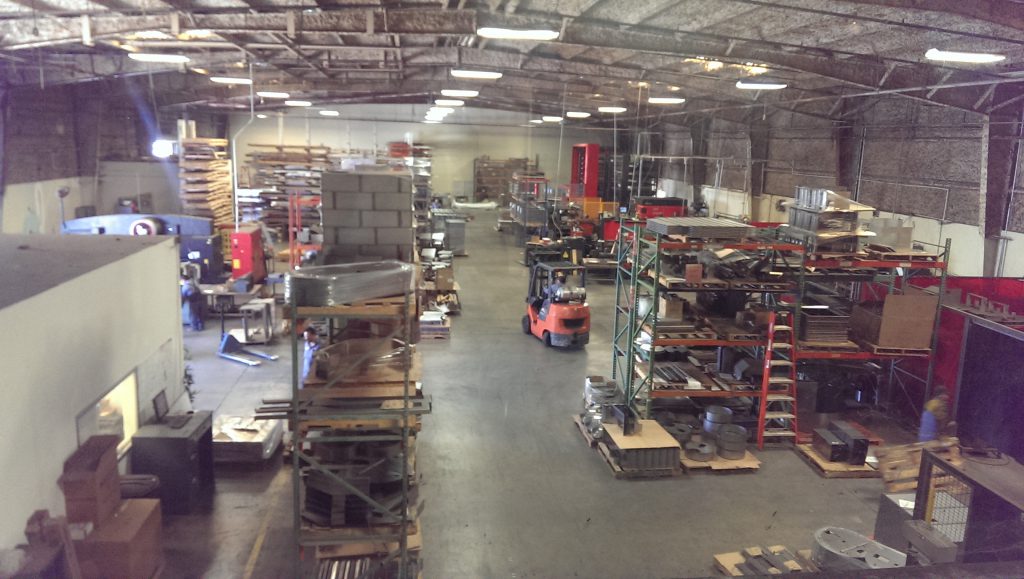
Ever wonder how many different parts are needed to make an airplane?
It takes a lot. Three million go into every Boeing 777, for instance, and it takes hundreds of suppliers to put it all together. Many of them look like Lock-Ridge Tool Co., a family-owned sheet metal fabrication and assembly firm that supplies parts to companies the trucking, aerospace, computer, and aviation industries. Lock-Ridge started as a one-man operation in a Southern California garage in 1962. Today, the Pomona-based company employs over 70 people.
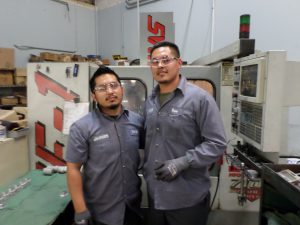
Business hasn’t always been easy. Around 2000, the company automated a lot of its processes and implemented a lean manufacturing strategy in order to keep costs down and remain competitive against both foreign and domestic rivals. But it ultimately survived; and in 2013 Lock-Ridge moved into its 60,000 square-foot facility in Pomona where it bends, stamps, tools, laser-cuts and welds sheet metal for the bits and pieces in all sorts of stuff.
And, according to a spokesperson, all of the material inputs it uses and the equipment on its shop floor is American-made. Says Lock-Ridge’s Mallory Lipert:
We use domestic sourcing for all of our materials. We buy all of our equipment from U.S. suppliers and manufacturers. Many people do not realize where the products that they use every day come from. It’s really important that Americans are educated on this, because we do not want the skills trade to go away.
Very cool. Check out Lock-Ridge’s Mfg Day 2014 video, and see some of the faces behind the art that is American manufacturing.