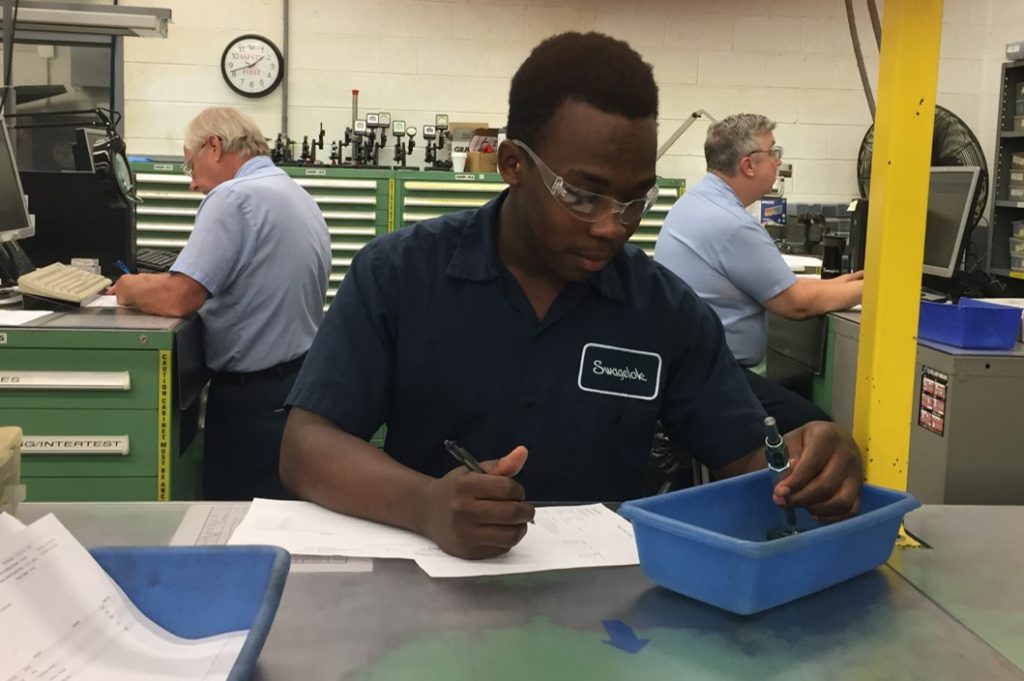
It’s a win-win: Students train to earn good-paying jobs. Employers get skilled workers.
Right now, there are more than 4,000 advanced manufacturing jobs available in Northeast Ohio. By 2030, there could very well be 50,000 of these jobs.
Who is going to fill them?
Figuring out how best to recruit and train young people for the factory jobs of the future is one of the biggest questions facing the manufacturing sector. Baby boomers are retiring, after all, and many employers say there aren’t enough workers out there with the skills needed for these high-tech roles.
Enter the Manufacturing Extension Partnership (MEP).
This federal, state and locally funded program is aiming to build the skilled workforce that so many manufactures say they need. Backed with funding and support from America’s manufacturing companies, the MEPs are reaching out to high school students to teach them that today’s factory gigs are not the dark, dirty, and dangerous jobs of decades past.
One such program is the Northeast Ohio MEP, which is run by the Manufacturing Advocacy and Growth Network (MAGNET) in Cleveland. MAGNET offers many services to small and medium-sized businesses, including consulting, training, strategies, cost saving and management practices.
But more importantly, the program is solidifying its work with a robust apprenticeship training program that starts with area high school students.
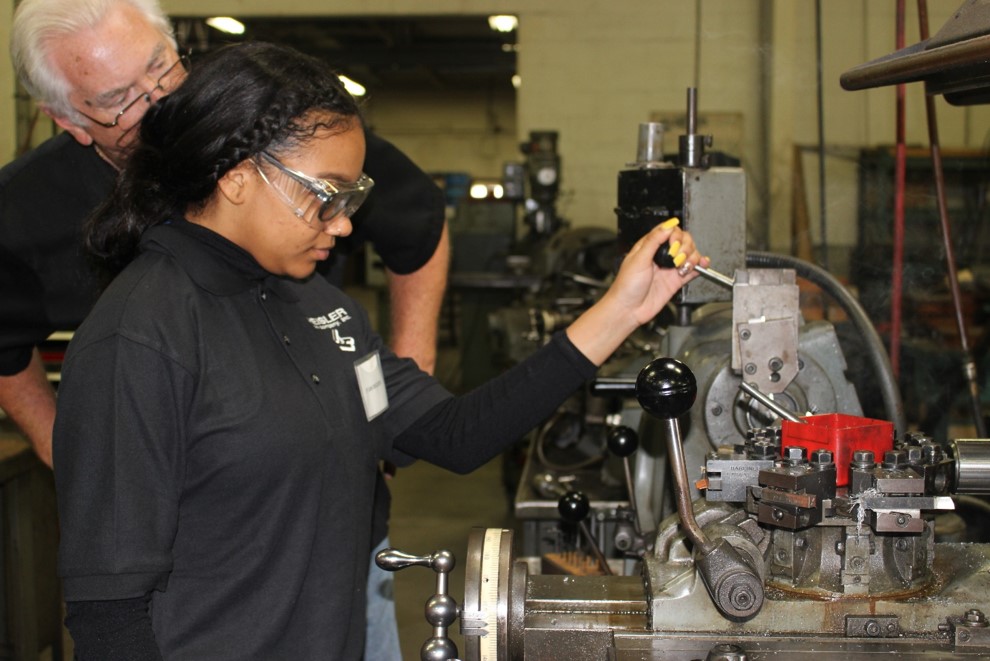
The students begin learning about advanced manufacturing when they enter the ninth grade and are introduced to robots, 3D printers, artificial intelligence and other cutting-edge techniques. By the time they become high school juniors and seniors, the students can move into paid internships with many local area manufacturing companies — and that is where the most important work happens.
“When they graduate, they already have a skill and know the people at the company and feel good about it, and might take that full-time job when they graduate,” said Mike O’Donnell, vice president of operations at MAGNET. “The real spirit of these programs is that they are obviously going to gain job skills, but it helps them socialize and understand manufacturing, so they are ready to go to work right when they graduate from high school.”
Students work two days a week at a manufacturing facility while also attending high school. The manufacturing companies invest in these trainees and reimburse the program half of the labor cost when the internship program is completed by high school grads.
Manufacturing Connections
MAGNET’s MEP program offers summer internships for younger students, but its advanced apprenticeship program is what sets high school students on an accelerated career path.
“We call it Early College, Early Career (ECEC),” O’Donnell said. “This program is more robust. We think long-term it can have a major impact in Northeast Ohio. How the program works is they can graduate as a senior and at the same time they can get 20 hours per week working at a manufacturer that’s been pre-qualified in this program.
“These manufacturers run great shops with opportunities for advancement and when you graduate you will probably be guaranteed a job at the company. They get college credits for their time and in the summer, they get full-time work.
“They don’t get paid the sort of minimum manufacturing wage like $17-an-hour for an entry-level position. They can make some pretty good money. I would say in the $20-an-hour-and-up range because they are skilled and know how to operate a machine, computers and some tool and die.”
There are currently 90 students in the ECEC program and approximately 130 students who go through the Ohio MEP internship program at career tech high schools each year. Many of these students are recruited from schools in low-income neighborhoods where career opportunities are limited.
“If you are 40 or 50 years old and welding or running a CNC machine, you are all set. But how do you replace them when you need new workers for growth? That’s the challenge that our ECEC is really starting to get some traction on in the apprenticeship program.” Mike O’Donnell
Many of the ECEC students would not even know the MEP program exists without the education and recruitment from MAGNET.
“Typically, we would target at-risk high schools and their students, because the program fits well for kids that don’t find a home,” O’Donnell said. “They don’t go to college and if they do go to college, it might not be right for them in terms of their skill set. And then they sort of opt into this.
“One of the key elements that’s important is the sustainability issue to it. It’s very sustainable and the companies want to do it. Each year we graduate 50 to 80 students per semester, and it is being ratcheted up to figure out how we can get more companies involved even though they are already very involved. We want to solve some of those sustainability issues, and this is a major part of what MAGNET does.
“The target to starting the program went to the regions where there was the most need. In some of the distressed inner cities. Later it would expand but right now there are plenty of schools that are great where the MEP program could provide them with a great career path.
“Maybe a student is not at risk right now as a junior, but they could be at risk when they graduate as a senior with no job. That is a horrible place to be as a senior. You get out, you graduate high school and you have no place to go. You have no job; you have no money. But that’s what we are trying to solve, that they can land on their feet and get a good job.”
Honorable Work
A core piece of MAGNET’s mission is to ensure manufacturers have the skilled workers they need to grow. Part of that solution is to upskill existing workers, including people who are out of work, looking for a change or a just underemployed.
In 2017, the MEP National Network connected with 26,313 manufacturers, leading to $12.6 billion in sales, $1.7 billion in cost savings, $3.5 billion in new client investments and helped create and retain more than 100,000 manufacturing jobs.
MAGNET is also leading the development of numerous community college offerings called “fast-track training” for in-demand occupations including CNC (computer numerical control) machining and welding.
But the ECEC program is the wave of the future to prepare students with the skills needed to thrive in an expanding advanced manufacturing industry.
“If you can run a CNC machine or weld right now, you are in,” O’Donnell said. “They can’t train enough welders right now. If you are a welder and you are certified, there is no stopping you. Try to find a good welder. If you are 40 or 50 years old and welding or running a CNC machine, you are all set. But how do you replace them when you need new workers for growth? That’s the challenge that our ECEC is really starting to get some traction on in the apprenticeship program.”
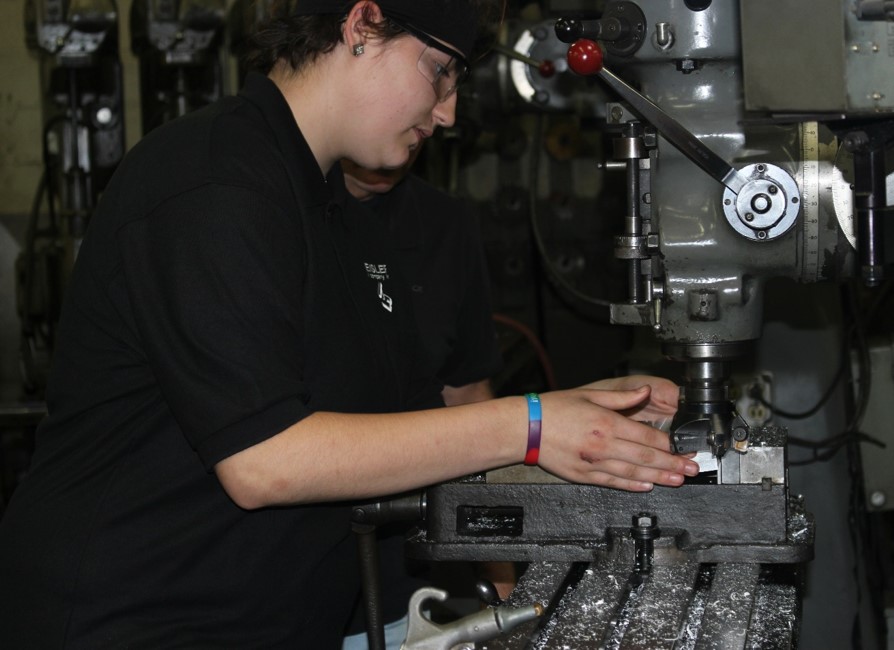
There are approximately 55 MEPs in the United States. Every major American city has a MEP program and more training will be needed to meet the future demands of American manufacturing. The government knows it, the manufacturing companies know it, and the workers know it. Working together, America can create a new generation of skilled workers to meet our future demands of building things.
“This is as honorable work as any other work I can think of,” O’Donnell said. “Every job in manufacturing you gain multiple jobs because you have a supply chain, and you have restaurants where people are spending their money. If you just open another Walmart, you are not generating any additional jobs.
“We at MAGNET and all the other MEPs know that manufacturing is honorable work. It’s as honorable as a lawyer, it’s as honorable as a doctor. Parents want to do the best for their kids, and they should know you can do very well in manufacturing.
“This is not for MAGNET or just Northeast Ohio, this is for the United States. We need to be competitive to protect our standard of living here.”