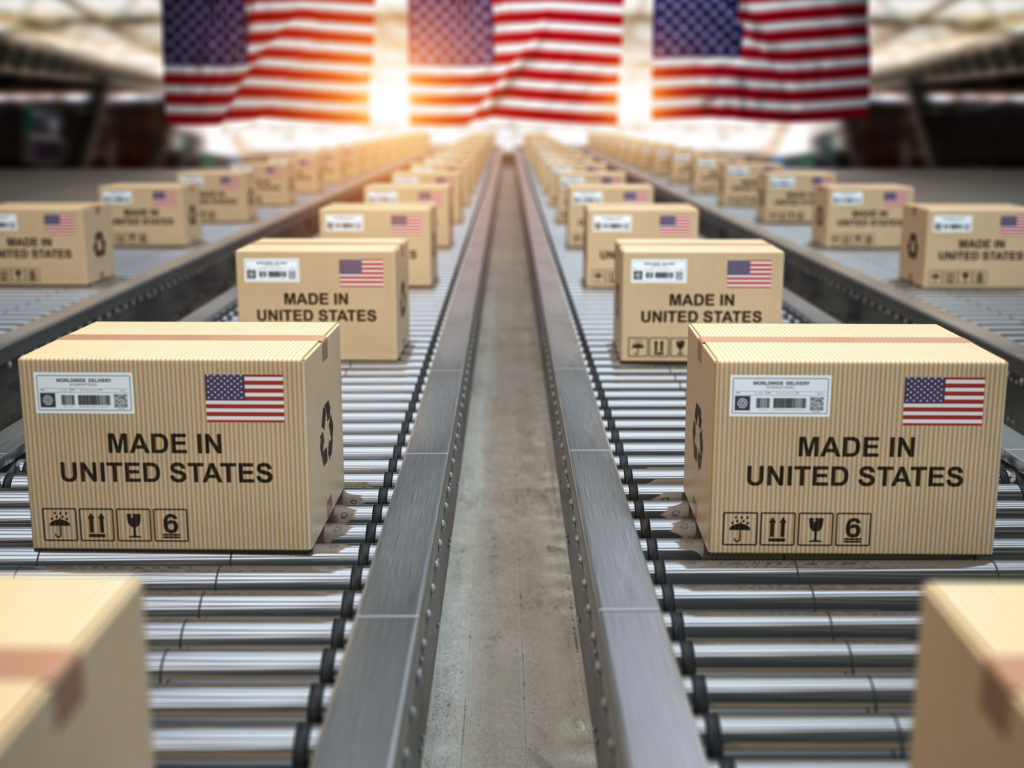
“Doing nothing may not be an option,” writes the management consultancy.
“You don’t need a weatherman to know which way the wind blows,” said Bob Dylan.
You could say that about the prospects for U.S. manufacturing in recent years, as deteriorating relations between the Chinese and U.S. governments coupled with a pandemic that has made long trade routes unreliable to greatly increase the American public’s appetite for reliably produced and sourced goods. People are into Made In America. It’s politically popular, and so is reshoring.
But in McKinsey & Associates, the ubiquitous management consultancy that has been cranking out reports on business efficiency since the 1920s, we have a reliable weatherman. McKinsey has long recognized the U.S. manufacturing sector’s outsized contribution to the nation’s economic productivity growth, exports, and private-sector research and development.
It hasn’t always been sold on U.S. manufacturing sector as a desirable vehicle for mass employment, nor has it been in localizing more manufacturing activity in the United States.
But that was then, and this is now, and it didn’t have the U.S.-China trade fight and the pandemic to consider. So now, we get a new McKinsey report. “US manufacturing has reached an inflection point,” its authors argue, and it cites the slow clawback of factory jobs lost en masse in the decade after Washington normalized trade relations with the Chinese government, as well as manufacturing’s stabilized shares of global manufacturing GDP, output, and exports.
The winds have changed. And now, these McKinsey guys say, manufacturing can grow. And it probably should. The authors write:
A strong manufacturing economy unlocks important employment and advancement opportunities — a factor set to grow in significance if current job market pressures ease. Manufacturing is the main economic engine and primary employer in around 500 US counties today, and in those communities, the industry employs a broader-than-average swath of the overall population and does so more inclusively.
So, what will determine how much of an inflection point (to use McKinsey’s term) this current moment is? It will be determined by the level of effort manufacturers and U.S. policymakers put into making manufacturing “more sustainable, more digital, more skilled, and more resilient.”
“More sustainable” refers to environmental sustainability, and the report points out that manufacturing by and large has relied on fossil fuel energy since the Industrial Revolution. But! Because we’re poised for a society-wide energy shift, manufacturing is presented with an opportunity: Demand for renewable energy equipment is incredibly high and recently passed industrial policies will make capital available so that manufacturers can make this stuff.
“More digital” is a way of saying “make manufacturing more automated” to improve efficiency and productivity, while “more skilled” means realigning worker skills to the realities of the jobs that will be coming online. This is the kinda thing you find in a McKinsey report on manufacturing all the time. “McKinsey research,” they write, “projects that by 2030, the share of physical and manual tasks in the overall economy will have fallen by about 27 percent since 2016, replaced by greatly increased demand for technological and cognitive skills.”
But “more resilient” is the big one here, as McKinsey is basically calling for shorter supply chains to minimize the risks of production disruptions. By its own own analysis, shifts in the name of resiliency could move more than $4.5 trillion in trade in the next five years, and the authors point to the consultancy’s own surveys of business executives that say supply chain localization is a trend likely to continue.
So what’s the takeaway for McKinsey?
More localized production is going to happen, because “doing nothing may not be an option.” They write:
Our analysis of the supply chain of a hypothetical midsize US consumer electronics company with a highly globalized production network suggests that rising factor costs over the next seven years are likely to erode the company’s margins by six percentage points. Accounting for the costs of carbon emissions and likely supply chain risks would depress margins by a further five points. Even aggressive levels of automation would still leave the manufacturer with a seven-point margin reduction.
And this, this necessary supply chain reorientation to prioritize resiliency, is going to be a huge issue for businesses. “Large-scale changes to manufacturing processes and footprints may take ten or 20 years,” they write, “and breaking away from the status quo will require creativity, commitment, and significant innovation. The remit for any such plan can only fall to the CEO.”
If a well-established management consultancy is writing this kinda stuff, the wind is indeed blowing in domestic manufacturing’s direction.