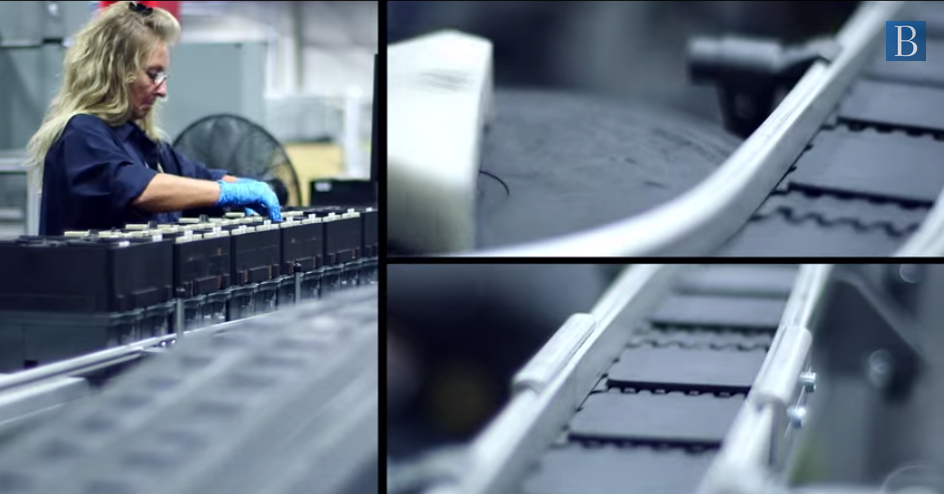
These industries will drive the future economy, according to a new Brookings Institute report.
Nearly three dozen manufacturing industries are crucial to America’s future economic prosperity and wage growth — but we’ve got to get to work to ensure they can succeed.
A new report from the Metropolitan Policy Program at the Bookings Institute identifies 50 high-technology innovation industries — 35 of which are in manufacturing — as the “central component of any future revitalized U.S. economy.” These industries are defined as having a “deep involvement” in technology research and development and STEM (science, technology, engineering, and math).
“These industries punch way above their weight,” said Bruce Katz, vice president and founding director of the Metropolitan Policy Program, during a Brookings event on Thursday. “These are the industries that have driven the American economy forward. … They’re not just supplying jobs. They’re supplying good jobs with good wages.”
But these industries need support to succeed over the long-term, including a strong skills pipeline to supply much-needed STEM workers; a commitment to strong innovation; and an ecosystem that brings government, large firms, small businesses, universities, community colleges, and others to compete globally, Katz and other speakers noted.
And we’ve got to get to work fast. The United States is losing ground to other nations on advanced industry competitiveness, as our negative trade balance in the sector shows. As the report notes:
“Although advanced industries export $1.1 trillion worth of goods and services each year and account for roughly 60 percent of total U.S. exports, the United States ran a $632 billion trade deficit in the sector in 2012.”
Things don’t appear to have gotten much better since then. New figures released from the Commerce Department on Thursday morning show that the overall monthly U.S. goods and services trade deficit widened to $46.6 billion in December. Imports hit $2.85 trillion in 2014, up 3.4 percent.
These deficits cost jobs — nearly 900,000 jobs in 2013 due to the trade deficit with Japan alone, for example.
Why Advanced Industries Matter
The rewards for supporting advanced industries are obvious. The 50 identified in the report employ 12.3 million U.S. workers — about 9 percent of total employment — and produce $2.7 trillion in value added annually, 17 percent of the U.S. gross domestic product. There’s also a huge wage premium. Since 1975, advanced industries have increased almost five times as fast as those in the overall economy, according to the report.
That mirrors similar findings from the Economic Policy Institute, which reported in January that full-time manufacturing jobs pay $3,700 more each year on average compared to those in other economic sectors.
Advanced industries tend to cluster in large metropolitan areas that have the overall infrastructure to support them and occur in a range of configurations. For example, cities such as Grand Rapids, Mich., and Portland, Ore., are home to automotive, semiconductor and aerospace manufacturing. Meanwhile, Bakersfield, Calif., and Oklahoma City., Okla., focus on energy sectors.
The state of Virginia in particular has been a leader in attracting advanced industries, with 442,000 residents employed in advanced manufacturing — roughly 11.2 percent of the state’s total employment, Katz noted. On average, these workers make $96,740 a year, compared to $53,030 for other sectors.
Virginia Gov. Terry McAuliffe said a focus on innovation, creativity and a “world-class infrastructure” is helping spur advanced industry job growth. The state also is putting emphasis on STEM education for elementary school students to encourage people to get interested in the field from a very young age.
“These are the future jobs, they’re here,” he said. “The metrics alone speak to it.”
Workforce Training Key to Success
When manufacturers are looking to open a new facility, they want to find the most strategic place to do so, several speakers said. And for many, finding key talent appeared to be the driving force.
Ron Armstrong, CEO of the trucking company PACCAR, noted that several factors impacted the decision to open an engine factory in Columbus, Mississippi in 2007, including easy access to suppliers. However, the location’s proximity to high-skilled workers sealed the deal.
The factory is located near Mississippi State University, which has a strong engineering program. But the area also has a robust community college system, allowing the company to train and hire tech-savvy workers.
Finding new talent is a key component of the Siemens Corporation’s efforts in Charlotte, N.C., said CEO Eric Spiegel. The company maintains a big presence in Germany, which has a strong apprenticeship system that drives its workforce. As a result, Siemens has 10,000 apprentices in Germany, Spiegel noted.
The company is trying to bring the apprenticeship model to its facilities in the U.S., including Charlotte, where it partners with a community college to train and hire new workers.
“You develop a real skill, you get a certificate… you have a real job and you have no debt,” Spiegel said of the apprentices. “It’s also a good avenue for building the next middle class.”
A skilled workforce also played into Stanley Black and Decker’s decision to reshore a power drill factory from China to a new facility on the North Carolina-South Carolina border, said CEO John Lundgren. At the time, the decision was mostly financial — along with the workers, there was a strong local component supply chain. Moving it to the United States also cut down on shipping time, which means products can get to thr market faster.
But what Stanley Black and Decker didn’t foresee was the “incredible support” from the public for producing a Made in America product, Lundgren said. “It’s been a great success,” he added.