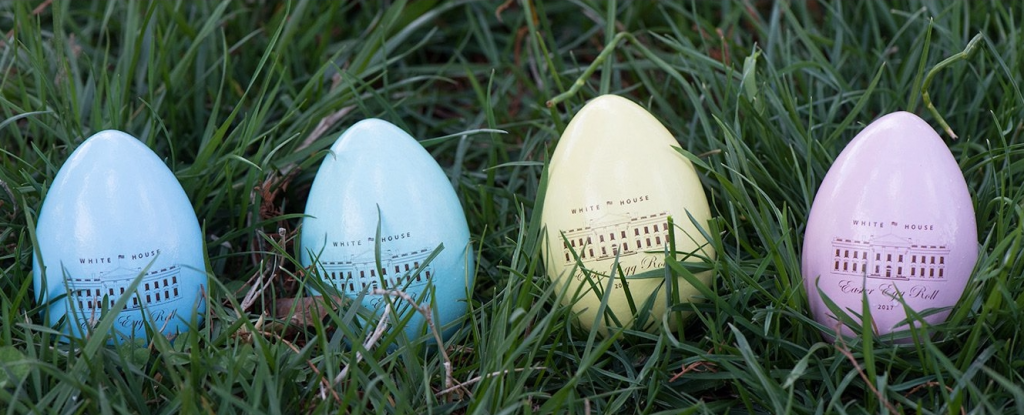
Wells Wood Turning & Finishing also creates everything from rolling pins to furniture parts.
Wells Wood Turning & Finishing has a variety of high-profile clients throughout the United States.
But none is more prominent than the White House.
The Maine company supplies the tens of thousands of wooden Easter eggs used in the annual White House Easter Egg Roll. This year’s event is scheduled for Monday, with a crowd of about 20,000 children and parents expected to scour the South Lawn for a special White House souvenir.
“Since our eggs for the White House get the most attention, for obvious reasons, for fun we’ve started calling ourselves America’s wooden egg supplier,” said Simon Varney, the co-owner of Wells Wood Turning & Finishing.
Wells Wood Turning & Finishing has manufactured the White House eggs since 2007. The White House eggs are made of solid yellow birch wood that is sourced in Maine, and the imprinted design on the eggs changes from year to year — although typically it carries the signature of the President and First Lady.
The company works directly with the First Lady’s office, also known as the White House Social Office, to come up with the design, Varney said. This year’s collection is pastels – pink, yellow, blue and green. And then there is the gold egg.
“The gold egg is like the piece de resistance,” said Varney. “This is the shiny egg this year. It’s just a shiny, high profile piece in the set.”
And then there was gold! So proud of the Wells team for their hard work in bringing this year's project to life. Love the #EasterEggRoll pic.twitter.com/kUQgmL34A3
— Wells Wood Turning (@WellsTurning) April 11, 2017
The first White House Easter Egg Roll took place in 1878 after President Rutherford B. Hayes agreed to open the White House grounds on Easter Monday to children who wanted to roll Easter eggs. This year’s celebration will be the 139th edition.
Former President Obama and First Lady Michelle Obama took the Easter Egg Roll to new heights during their eight years in the White House, including by bringing in popular musical acts like Justin Bieber and Ariana Grande to perform.
This year’s Easter Egg Roll is expected to be a much lower-key celebration. The New York Times reported that the White House has been doing some last-minute scrambling to put the roll together, since the First Lady is living in New York and her White House office has not been fully staffed.
The White House Social Office wound up purchasing 40,000 wooden eggs for this year's event (after some gentle prodding from Wells Wood Turning & Finishing). All children at the Easter Egg Roll will receive an official White House egg, but they can also be purchased via the White House Historical Association website.
To create the eggs, Wells Wood Turning & Finishing takes square pieces of wood and puts them on an automatic spool machine that in a matter of seconds turns the yellow birch into an egg shape. The egg-shaped wood is then put into a tumbler sander which contains sand paper. By tumbling the eggs against each other and the contact with the sand paper they become smooth as if each one was sanded by hand.
After the sanding process, the eggs move into the paint shop, where they are also placed into rolled tumblers and mixed with the paint color of choice. After drying, the eggs are then pad printed with the design requested by the First Lady’s office.
“It sounds a lot easier than it actually is,” said Varney. “It’s tricky to get the artwork just right during the pad printing. There is quality control every step of the way where we are inspecting a certain percentage of the eggs as they come through the process. They are then boxed up, put on a pallet, out the door and Happy Easter.”
“We Want to Keep it Made in Maine”
Varney and co-owner Chris Chandler purchased Wells Wood Turning & Finishing in November 2016. It is one of the few remaining wood turning mills in Maine. In the 1970s, most medium-sized towns in Maine had a wood turning factory. But from about 1990 to 2009, most of the wood mills were closed as business was outsourced to China.
But, for other than extremely large orders, it is no longer feasible to offshore the woodwork.
“That time was a tough time for wood production,” Varney said. “I believe a lot of the wood was outsourced and a lot of the production went overseas. Demand dried up for American manufacturers in terms of wood and a lot of mills didn’t make it.
“After 2012, 2013, I think the economy got a little bit better and I think there was some onshoring where demand is coming back. Customers are asking for American-made things. I think the pricing levels — whereas China had an advantage of some high percentage ten years ago — I think we are closer to parity now. When you have parity, I think people want closer to home, American-made, higher quality stuff. That’s the market dynamic now.
“Chris and I are really pleased and surprised at how much demand is out there.”
My partner and I are really big on manufacturing in Maine, so it’s a great thing to take over the mill and provide manufacturing jobs. We want to keep it made in Maine, made in America and be as innovative as we can be. Simon Varney, Wells Wood Turning & Finishing
The demand that keeps Wells Wood Turning & Finishing consistently producing product is not just centered on the wooden Easter egg market. The company makes a variety of products that are sold into the wholesale market under popular brand names, including rolling pins, napkin holders, miniature baseball bats, kitchen ware, and intricate furniture parts.
“It’s a wood turning mill, so basically we make anything round out of wood. Round is the key,” said Varney. “We don’t do flatware. Cutting boards, for example, isn’t something we do much of but anything round we can do. Rolling pins is a very good example. We have a pretty good reputation, in addition to providing eggs to all kinds of organizations, we’ve got a pretty good reputation for rolling pins as well.”
Wells Wood Turning & Finishing employs 30 people in its factory located about 50 miles northwest of Portland. The factory is equipped with various lathe and spooling machines that automatically carve the wood.
“These are pretty high capacity machines, so in the case of a spool machine you can probably crank out 10- to 12-thousand pieces a day,” said Varney. “We are just happy to have such steady business.
“My partner and I are really big on manufacturing in Maine, so it’s a great thing to take over the mill and provide manufacturing jobs. We want to keep it made in Maine, made in America and be as innovative as we can be.”