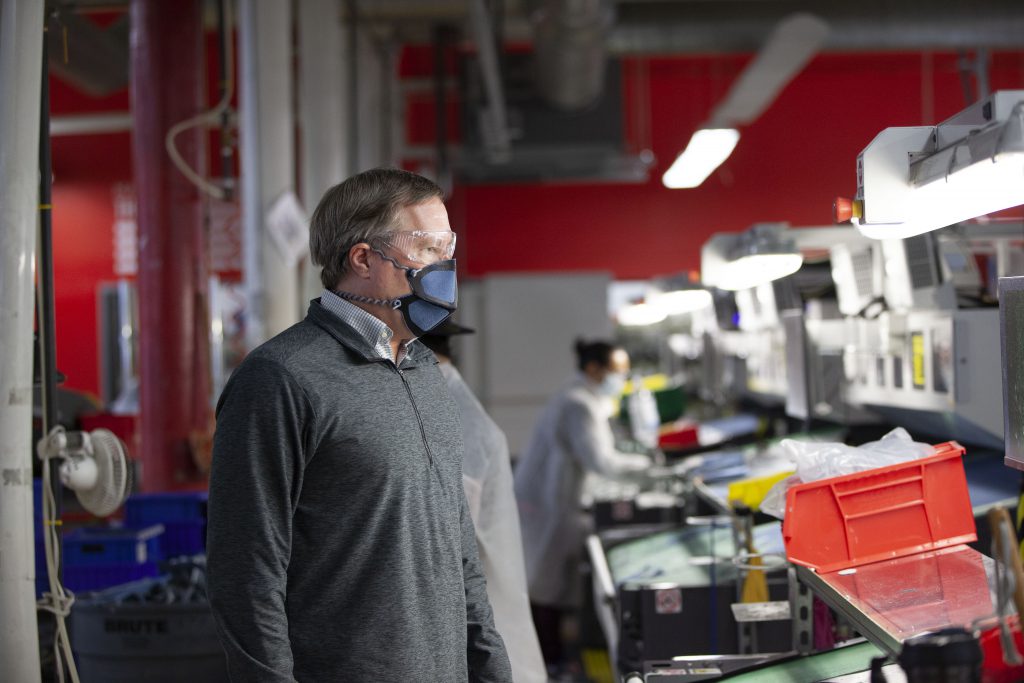
The New England company is using the same supply chain and techniques it uses to make its footwear.
New Balance makes its elite running and walking shoes at locations throughout the world, but unlike other major athletic shoe manufacturers, New Balance also has a domestic presence with five factories located in the New England region.
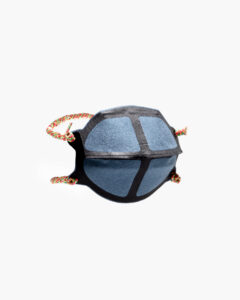
It’s the reason why the Boston-based New Balance has been able to quickly retool to make much-needed face masks to help in the response to the Coronavirus pandemic.
Two of the company’s manufacturing plants – one in Lawrence, Mass. and the other in Norridgewock, Maine – have halted shoe production and are making prime face masks for both medical workers and essential employees who are still at their jobs every day. As of today, its other three American locations are idle, but are available should the New Balance team increase production of personal protective equipment (PPE).
“By mid-April, our goal is to make up to 100,000 units weekly at our Lawrence, Massachusetts and Norridgewock, Maine factories combined,” New Balance owner and Chairman Jim Davis said in a statement. “We are simultaneously advancing our current face mask design and materials specifications to ideally meet FDA requirements and achieve a product that can be confidently used by frontline medical staff who require those criteria.”
New Balance offers an extensive line of Made in USA shoes manufactured at its five domestic factories, allowing the stalwart company to quickly pivot its product from shoes to face masks. No other major athletic footwear company has this Made in America capability. If mask production were to come from an overseas footwear company, there is no telling how long it would take for the product to reach Americans in need of facial protection to help ward off the Covid-19 virus.
Dave Wheeler is an executive vice president at New Balance. Wheeler has been instrumental in making the pivot to manufacturing face masks a reality.
Starting up mask production involved no major disruption in the New Balance supply chain, because making Made the USA footwear for decades has created reliable supply chain connections from fabric suppliers across America, Wheeler said.
“That really positions us, I think, far better than many other companies that started from scratch and pivoted over to PPE but had to start from scratch with their supply base,” Wheeler said. “We are really fortunate to be able to leverage our current supplier relationships and they all stepped up. I’ll tell you everybody wanted to make it happen and they worked day and night and through the weekends with us to get us samples and make sure we had the right volume. It was very inspirational.”
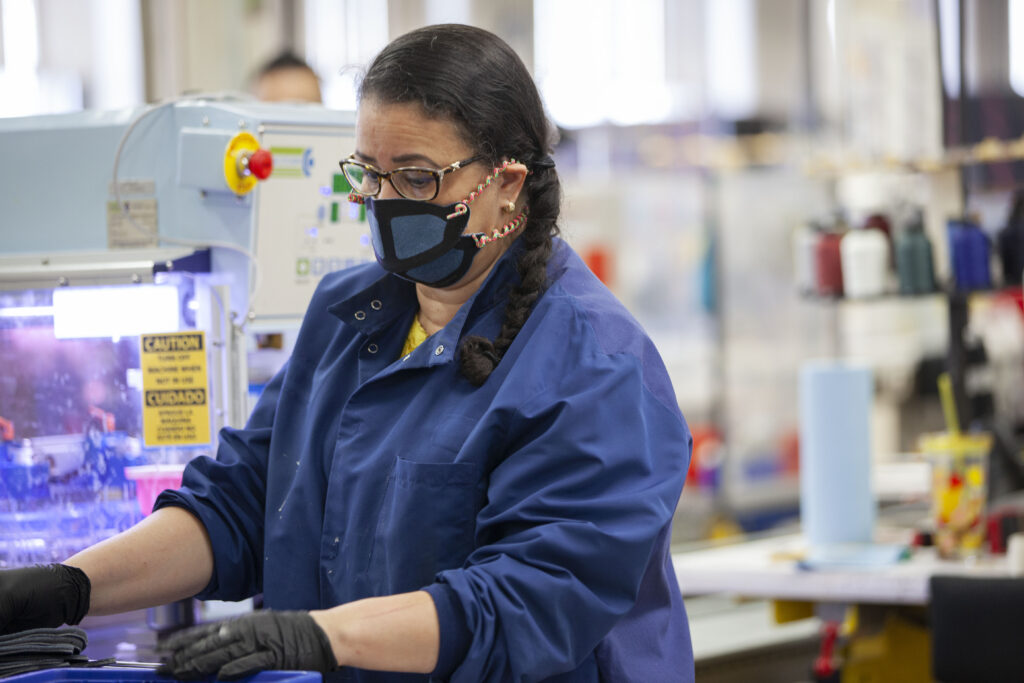
Wheeler put together a cross-functional team of experts on March 20, and one week later professional masks were rolling across production lines. The company started with two production lines and as of today now has 10 lines producing protective face gear.
“We wanted to make it right and didn’t want to just jump right into it making assumptions, so we spent quite a few hours that previous weekend with some experts at Mass General (Massachusetts General Hospital) and MIT (Massachusetts Institute of Technology),” Wheeler said. “We had an actual physical prototype that we could manufacture with our current assets, so that weekend was a pivotal time for us to move from footwear all the way over to production of masks, which we did on March 27.”
After consultation with the experts at Mass General and MIT, the New Balance team came up with a standard face mask that offers better filtration and fit than some of the cotton masks that are being mass produced by other companies or made by individuals in their homes.
The New Balance masks have five layers of protections, which are bonded together with a heat-melt process.
“The mask has a polyurethane foam layer. We call it fabric but it’s basically foam. There is a second piece next to it that is called non-woven melt-blown fabric. It is kind of sprayed on and is similar to a Swiffer material that is actually used in an N95 mask,” Wheeler said. “The Swiffer-type fabric creates really small pores and that is the filtration capability needed in melt-blown mask. Those two are really important elements of it.
“And then there is a set of nylon and polyester layers that are on the outer surfaces. So, all those layers are put together and put through a heat-melt process that creates what essentially looks like one piece of fabric.”
New Balance used its “no-sew fabric” on the masks, which is just what it sounds like – no sewing required. A similar technique to how New Balance makes its footwear, the no-sew fabric basically bonds the mask together.
That’s not the only similarity to the company’s shoes.
“We’ve also used our curly laces for the straps,” Wheeler said. “I think it is a neat enhancement because not only does it tie to our footwear heritage, but also it is a performance capability that doesn’t exist on other masks. The end of the laces come through the eyelets on the mask and once you put the mask on you can actually pull those shoelaces forward and it brings the mask tighter to your face so you get a better fit.
“We’ve received a lot of good feedback from healthcare providers that have used it.”
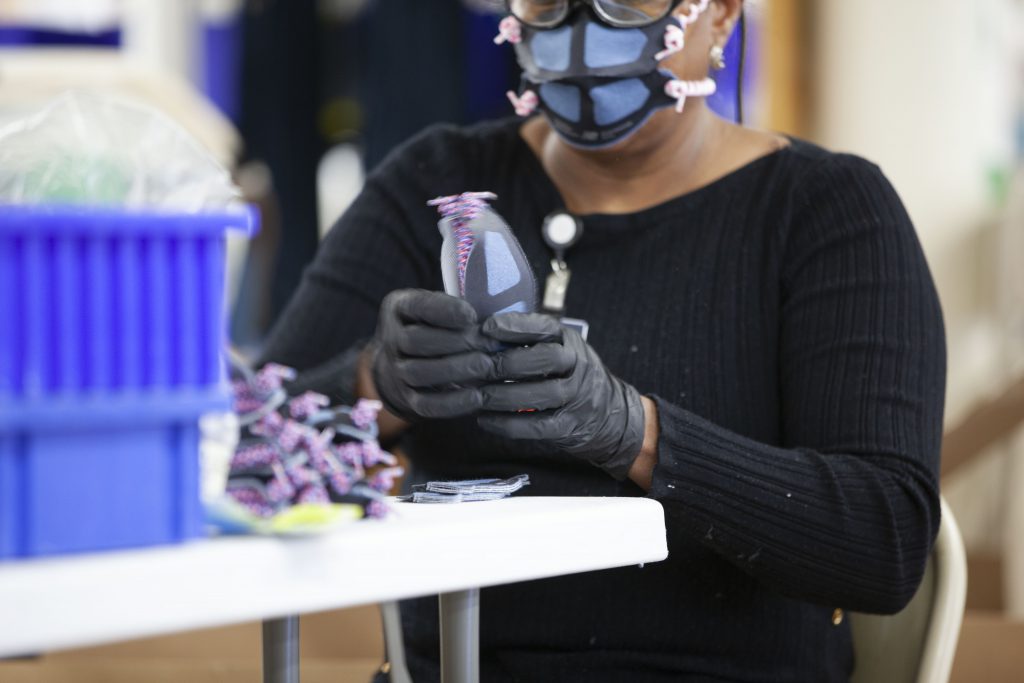
New Balance does not consider its mask production a commercial opportunity; the company is pursuing a break-even pricing policy or even donating the face masks. But mask making does allow the shoe manufacturer to keep a portion of its workforce employed while the Made in USA shoemaking operations are on hold.
The design of the masks matches up well with current New Balance equipment, so the company did not have to retrain its associates. There were, of course, changes in the layout at the two mask-making facilities, such as keeping workers six feet apart. Employees were also provided with hair bonnets, masks, gloves and gowns.
“That is not a normal manufacturing technique,” Wheeler said. “As you know, you want everything as tight as possible with as little movement as possible so that production moves quickly and there is not wasted time, but we went in the other direction because of the safety requirements.
“It has worked out just fine. We really didn’t see major disruption there and we certainly wanted to make sure we protected our associates with some physical PPE.”
The New Balance team is working diligently to create an even better mask that can be worn in surgical situations like the N95 respirator mask. And with the help of state and local governments in Massachusetts and Maine, they are researching other product lines such as disposable gowns and foot coverings.
Despite some calls to reopen the economy, the COVID-19 pandemic will likely be a major concern until a vaccine is developed. So even if the number of infections dramatically decreases and people are no longer isolated, it will be a “new normal” that will most certainly include the wearing of face masks wherever people congregate in large numbers.
The 100,000 face masks produced weekly by New Balance could even increase as there seems to be a never-ending demand for protection. And fortunately, the team at New Balance can quickly produce supplies right here in America.
“To make a last plug for U.S. manufacturing, we wouldn’t have been able to start from scratch and go into production within a week without U.S. manufacturing and all the expertise that comes along with it,” Wheeler said. “Whether that is design capabilities, material development, prototyping and all the engineering expertise to realign the production lines to make it work.
“So, when you look at the strength and value of U.S. manufacturing, I think it is a perfect example of being able to pivot from one product to another because it’s right here in your backyard. We were driving from Lawrence down to Boston at Mass General and MIT for testing on fit and fabric capabilities. It is a half-hour drive.
“When you think about other challenges from sourcing around the world it doesn’t get too much faster than that. In the need of where we are at right now, it’s a pretty awesome capability to have at hand and we are just humbled and fortunate to step up and make a difference.
“It’s been a great journey for us.”