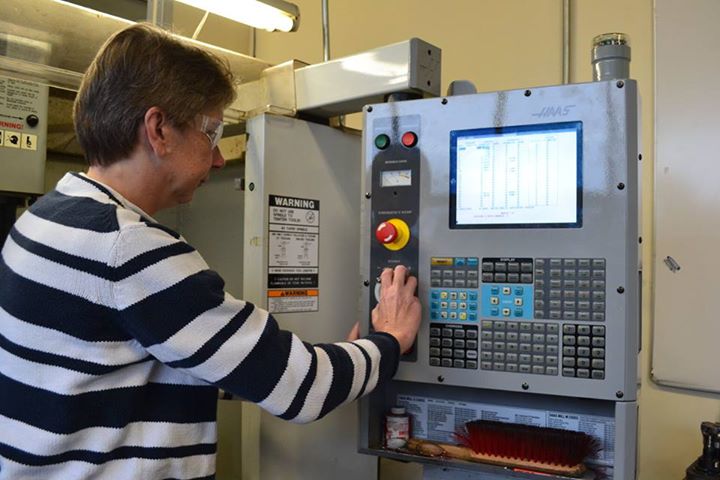
Program provides training, funding and support services for manufacturing workers of all ages.
Less than a year ago, 28-year-old Chicago resident Valerie Frost was floundering to find a job that would become a career.
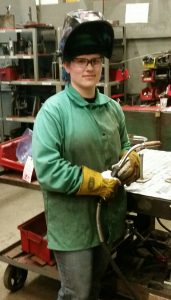
She worked for minimum wage at a dog hotel. She amassed $20,000 in student loans to train to become a cosmetologist and medical coder. But after short stints at each profession, she still couldn’t see herself doing those jobs for the rest of her life.
“I found it interesting to do stuff with my hands, and not just be stuck in an office or something,” Frost said.
Then Frost found the tandem of the Manufacturing Works program and the Jane Addams Resource Corporation (JARC). Manufacturing Works provided funding and counseling — and connected her to a new employer — while JARC administered the schooling for her career in manufacturing.
Frost is now into her fifth month as an American Welding Society certified welder.
“I knew I wanted to work with my hands and figured out I wanted to do something in manufacturing and I just found welding interesting,” she said. “I went over to Manufacturing Works to meet with them as part of the program, and they provided my funding at Jane Addams.”
Frost is optimistic about her welding job at S&C Electric in Chicago, which makes components for the smart grids of power companies across the globe.
“Jane Addams found me the job through Manufacturing Works,” Frost said. “I’m happy here. I’m really glad I found the school and the programs and everything. Manufacturing Works tries to find something you can get to that you want to do and not just throw you wherever. I think I will have a great career here.”
Manufacturing Works is a Chicago nonprofit workforce consultant team that provides workforce training, funding and support services for job seekers. Manufacturing Works is connected with many Chicago-area manufacturing businesses and graduates of job training schools in Cook County, Illinois, including the city of Chicago.
“I like to think it’s kind of a new innovative concept,” said Tony Garritano, director of Manufacturing Works. “It’s very unique to the region here in the Midwest. We are basically workforce consultants. Our mission is to work with manufacturing employers. My team has the luxury of not having to worry about retail or healthcare or anything like that. My team of job developers, account executives and case managers are able to focus solely on manufacturing.”
Manufacturing Works acts as an intermediary between employers and various groups that have job seekers, including from high schools, colleges, technical training programs, veterans groups and a variety of workforce programs.
“We are able to ultimately make sure we are screening them and assessing them properly, because we know the specific requirements for those particular jobs from our employer partners,” Garritano said. “We are like a clearing house for the entire system of candidates specific to manufacturing.”
It’s not just younger workers like Frost who Manufacturing Works helps, either.
Judy Long of Chicago already had a long career in manufacturing before coming to Manufacturing Works. But her 18 years of experience were in the front office of a tack-cloth manufacturing facility doing customer service, accounts payable and accounts receivable. She was laid off after the company idled production for seven months and lost most of its customers.
“I worked in manufacturing since I graduated from college, but I was always front end,” Long said. “I was always fascinated by the equipment so when I got laid off I thought that I would go learn to operate the equipment.”
Long trained with the Jane Addams Resource Corporation to learn the skills to do hands-on manufacturing work. She was referred to Manufacturing Works to see if she qualified for funding to learn how to operate computer numerical control (CNC), a computer controlled system of manufacturing equipment used in most major manufacturing plants today.
Long, who lives about a mile from Wrigley Field on Chicago’s north side, was also concerned about the transition but realized she wanted, like Frost, to do hands-on work.
“I was thinking nobody wants to hire a 47-year-old woman that worked more than 18 years at one job,” she said. “Without Manufacturing Works and Jane Addams, I don’t know where I’d be at. I’d probably still be scrambling to find a job.”
With her manufacturing skills training and placement from Manufacturing Works, she is now employed at Flexan, a custom rubber molding company based in Chicago. Long is working in the finishing department, cutting off the excess rubber known as flash and has other responsibilities that need to be done before the rubber molding is inspected.
“Manufacturing Works places you at companies that provide good benefits and potential for promotions and raises,” Long said. “Even with automation, you still need people to run the machines. This is a place I think I can retire from.”
When Long finishes up her duties in the shorthanded mold finishing department, she will most likely begin running a mold press using her CNC training.
“It has made a big difference in my life. It's just been a positive experience,” she said.
A History of Helping
Manufacturing Works differs from other workforce center organizations in the United States in that other groups must know about every different industry that is hiring skilled workers. Manufacturing Works has the luxury of focusing on just one sector – manufacturing – and defines what it means to be a metals manufacturer, plastics manufacturer or any other type of manufacturing industry looking for skilled labor.
“A good thing about Manufacturing Works is we serve on many, many advisory boards and committees because at any given time, myself or my account executives represent 30 to 40 different companies with about 100 different kind of manufacturing job openings,” Garritano said. “So we are able to plug in quite nicely. They know we serve as a gateway to a lot of employers.”
Manufacturing Works began in 2005 out of a program of Instituto Del Progreso Latino, a community based organization in Chicago that has worked in education and workforce development for the past 38 years.
Instituto Del Progreso Latino had been providing a specific Chicago Latino community workforce development and support services when it was commissioned to do a project for the city of Chicago in 2002. Instituto was working with three other workforce development groups assigned to develop Ford Motor Company’s Ford Supplier Park, located across the street from the Ford Assembly Plant on the south side of Chicago. The supplier park consisted of 11 tier-one Ford suppliers.
“We were able to place the lion’s share of all those people that went into those 11 different companies,” Garritano said. “At that point the city government said, ‘Hey, you guys do this pretty well. We’re actually putting out a request for proposal to operate what we are going to call the Sector Center throughout Chicago and Cook County.’ So Instituto put a bid out and the bid was taken and we began operating in 2005. So Manufacturing Works is what came out of it.”
Garritano believes the Ford supplier project and the model of workforce development is what has made the program successful.
“We have a pretty big workforce system already in hand, but our job is really insuring the job seeker that comes off social services or unemployment, we will get them back to work,” he said. “The Manufacturing Works program in itself is a challenge to the system by allowing people direct contact with employers to gain real in-depth understanding of their specific business in an effort to consult with them or provide them options for whatever their specific workforce development need is currently.”
Having an employer bank of available jobs can only provide Manufacturing Works with limited information. They need the skilled job-seekers whom they can match with the job openings so it is a win-win situation for both employer and employee.
“The beauty of Manufacturing Works is that we are totally agnostic to any particular group,” Garritano said. “What we want to do is work with everybody and everyone to find the next best candidate so we are not specific to unemployed workers or ex-offenders or limited-English speaking candidates.
“That allows us the ability to be of great use to employers. The workforce search has a lot of different entities. So when we get job orders, we disseminate that to probably about 250 different entities at any given time. The training programs or employers can send us people and we screen them and do our due diligence to make sure they are the right candidate for the employer.”
“Manufacturing Works places you at companies that provide good benefits and potential for promotions and raises. Even with automation, you still need people to run the machines. This is a place I think I can retire from.” Judy Long
Valerie Frost was interviewed and tested by Manufacturing Works to find out if she was qualified for the program. Once accepted, her contact with her account executive didn’t end there.
“They provide the funding until you have a job,” she said. “They were calling to check up on my training and to inquire if I had the job I was referred to. They followed through to see how it was going and they still continue to follow up to make sure everything is fine.
“They all seem to really care over there and at JARC they all seem to really want you to do well and succeed and try to help you in whatever way they can.”
At the Jane Addams vocational training program, Long was trained in CNC to operate machinery, although she has not had the chance to implement her new skill yet at Flexan.
“It was really strange,” Long said. “Manufacturing Works, Jane Addams and a couple of other places were all working together to get me the job. Manufacturing Works provided funding. I wasn’t the only one that got their funding for the Jane Addams program. They also do resume help and providing job leads so that people can get jobs in manufacturing.
“And along with the CNC training I got at Jane Addams, they also provide a career management course where they also help you fresh up your resume and brush up on your interview skills. They also have welding training, press break training and they do job placement services. It was like Manufacturing Works worked as a team with Jane Addams.”
Manufacturing Works will accept anyone who is on the right track who is looking to become a productive member of society and meet the qualifications, Garritano noted.
“We place people with felonies,” he said. “They can come in to talk to one of the account executives, the same person that went to the employer and got their trust, walked the shop floor and understands all the specifics and requirements. They then give the job-seeker a test, reviews, help with a resume or do one-on-one screening to make sure that person is most appropriate.”
Manufacturing Works not only provides grants to the job-seekers but to employers. If someone is looking for a specific kind of manufacturing training, Garritano’s team can register them into programs like the Workforce Investment Act (WIA).
“We have the ability to get people registered under our program as well which is a big plus because often times people do not seek out higher-level training is they don’t have a way to pay for it,” he said.
If it wasn’t for Manufacturing Works, Valerie Frost wouldn’t have had the ability to pay for training as a welder. There is a tremendous shortage of talented welders in manufacturing plants across America. A talented, experienced welder today can earn an annual salary of as much as $100,000 to $120,000.
Frost is nowhere near that point, but has guaranteed, steady work with plenty of overtime. As she gains further experience, her pay will increase and the company will pay for her education if she decides to go into management.
Frost noted that she had never worked with metals before she started the program. But now she is most happy working with her hands — despite the fact her welding gloves were not sized for a petite woman.
“They said, ‘Hey, you’re not bad at it. It sounds like something you should keep doing,’” she said.