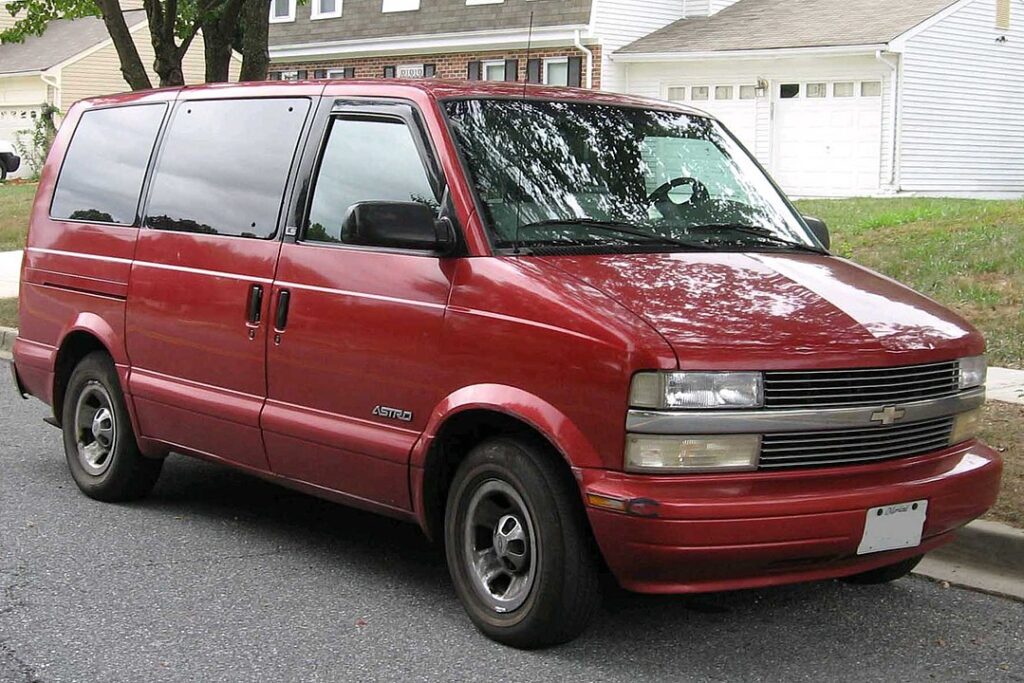
The company’s shift to EV production is an example in action of the dynamism that manufacturing demands.
General Motors recently announced that all of its light duty vehicles will be emissions-free by 2035. That means a lot more electric vehicles (EVs) coming this way and soon; the company already revealed a redesigned Chevy Bolt and a Chevy Bolt SUV.
This is all well and good. I’m married and have a couple of small kids, and we’re rapidly outgrowing our sedan. So I want an electric Astro van, pronto. I’ll even pay extra if they throw in the mid-90s upholstery so I can immediately dump an entire Big Gulp into the back seat so I can really relive my youth.
But it hasn’t been easy getting here. GM employs approximately 100,000 workers worldwide, and the decisions it makes about site selection and staffing are deeply affecting. Like, for instance, when it closed its plant in Lordstown, Ohio and most of the 1,600 workers there had to disperse across the United States to hold onto their jobs. They were among thousands of workers who faced a similar choice when the company announced this reorganization in late 2018.
Saying it’s not easy to lose your job or uproot yourself (and potentially your family) in response to “accommodate shifting consumer tastes” is an understatement. But other shifts are driven by technological and environmental progress. Yes, the things the auto industry makes – vehicles with combustion engines – must change for the sake of the planet, but those shifts are also opportunities.
That’s why a startup bought GM’s Lordstown facility and is beginning to produce an all-electric pickup truck that it’s marketing as a commercial fleet vehicle. The United Autoworkers appreciate this opportunity, too, and made it a point in contract negotiations to save the GM Detroit Hamtramck plant from shuttering. That’s (at least one big reason) why the company is putting $2.2 billion into gutting and rebuilding the factory so that it will serve as its center for electric vehicle manufacturing. GM’s calling it “Factory Zero.”
The GM executive responsible for the Hamtramck plant’s refurbishment recently spoke with the Wall Street Journal, and the interview provides an interesting look at how the company is managing this big pivot to EVs.
The whole thing is worth a read. But here’s a Q&A on the nature of auto manufacturing work, automation, and the future of the company’s workforce:
Q: Given that EVs require less manpower (to build than gas cars because their design is less complex), should workers be worried about there being fewer auto factory jobs in that future?
GERALD JOHNSON: I think every GM employee should be excited about what we’re doing. Because we see our EV strategy in total as a full-on growth strategy. We will expand. Yes, some job assignments will change, but we will have opportunities for everyone to come along with us as we make this transformation. There will be more work available in that future than what we have today.
That tracks closely with how the Alliance for American Manufacturing (AAM) thinks about automation: The robots are coming, but we shouldn’t fear them. Manufacturing will always require workers. We just need to make sure a lot of that work is done by American workers. There are plenty of public policy proposals that would help ensure that happens. You can read about the ones AAM has put forward here.