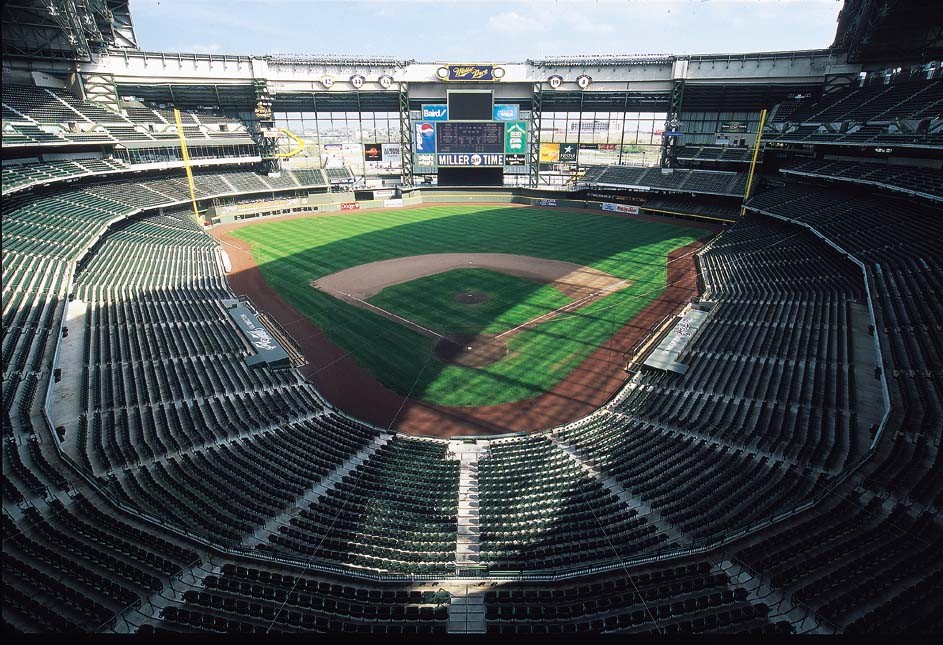
No matter where you live in America, you have probably sat in an American Seating Company seat.
A capacity crowd of 82,529 rabid football fans filled the seats at MetLife Stadium in East Rutherford, New Jersey on Feb. 2, 2014 for Super Bowl XLVIII. But there was a lot more sitting than the typical standing and cheering for the National Football League’s preeminent game, as the Seattle Seahawks drubbed the Denver Broncos, 43-8.
Many depressed Broncos fans, who paid a face-value price of anywhere from $500 to $2,600 per ticket, were not about to just get up and leave without taking in all the merriment a Super Bowl extravaganza provides. So they sat and watched.
What they didn’t know was they were sitting in a seat built by the oldest manufacturer of seating in the country. American Seating Company was founded as Grand Rapids School Furniture in 1886, and is still producing American-made products 128 years later.
In the mid-1800s, Grand Rapids, Michigan had an unprecedented reputation as the maker of the finest furniture in the United States, if not the world. But cheaper labor and the loss of the old-world craftsmanship moved furniture production to other regions of the United States.
Despite this mass exodus of household furniture makers, this was just the beginning for American Seating. In 1906, the company developed the first tilt-back opera chair and officially changed its name to the present-day American Seating Company.
This company would become ubiquitous with American culture in the 20th century, its products present at countless historic sporting moments and even one of the great life-changing events of our time: On December 1, 1955 in Montgomery, Alabama, an African-American woman refused to relinquish American Seating City Bus Service seat 1221 so a white person could sit down.
That woman was Rosa Parks. Her refusal, and subsequent arrest, became a profound symbol of the modern civil rights movement.
We’re pretty proud that we’ve been doing that for more than 125 years, right here in the same location, right here with a Grand Rapids, Michigan, Made in America workforce. Tom Bush, American Seating Company
The success of its student desk-chair unit and its introduction of the tilt-back opera seat helped the company expand over the years into business, entertainment, sports, office, and transportation seating. So many major league sports stadiums, arenas, and concert halls are outfitted with American Seating products that it’s easy to overlook that transportation seating is its top produced and purchased product.
American Seating bus seats, light-rail seating, and other forms of public transportation easily meet the Federal Transit Administration’s requirements for federal funding under the Buy America Act. Just 60 percent of the cost of all components of the product may receive federal funds when the steel, iron, and manufactured goods used in the project are produced in the U.S. Additionally, final Assembly must take place in the United States.
Because of this capability, American Seating dominates the market when metropolitan areas order new modes of transportation.
“We have a few pieces and parts that are sourced overseas but I think our lowest U.S. content product is in the high 80 to low 90 percent range,” said David McLaughlin, vice president and general sales manager of American Seating. “Virtually everything except for a couple of hardware items and foreign customer-specified fabrics would be the only things we don’t get from Michigan and four or five other states that surround us.”
American Seating is enthusiastic to be known as a Made in Michigan and Made in America Company. But that commitment didn’t come by accident.
“We’re right in the middle of an auto-oriented environment and we therefore have a lot of suppliers of plastics and metal parts and adequate labor,” McLaughlin said. “I think it’s safe to say right now if you were to compare our cost of manufacturing compared to what it was five or 10 years ago, as a percentage of sales, actually it’s probably dropped. We compete against companies that do a great deal of offshore sourcing, specifically China and Mexico. And yet I think we’ve been holding our own partially through innovation, partially because of the manufacturing base.”
The Buy America provisions can be a sore spot for a lot of companies. They can meet today’s FTA requirements by building an assembly plant in America, but there are questions about a cost-effective supply chain and labor pool. Many wonder if there will be an American market ripe for future investments.
“I had a phone call, oh, a month ago from one of our good customers that happens to be a Canadian bus builder,” McLaughlin said. “Well, the question to me was, ‘how much time will it take and how much will it affect your price on average if Buy America has to go to 70, 80, 90 or 100 percent?’ So I sarcastically said to the guy, ‘how much time do I have to come up with the answer?’
“He says it’s a complex question and I really need it in the next two months. I said I can give you the answer by the end of today, which I did. What I said to him is we are already at 90 percent and to get to 100 we have to change a small set of parts and hardware items. We have a domestic source all lined up for those items and it would take about three months to pull that trigger and get it done and the impact on the price would be little or nothing.
“Monday of that following week, he calls me back and said he asked my competitor on the same day what he asked me, and he didn’t know when he could get back to him.”
We run two shifts in this plant and sometimes a skeleton of two shifts at the other plant. We’re here to get the job done and get the stuff out the door. Brad Wilson, American Seating Company
American Seating Company didn’t get to where it is today by, well, sitting on its laurels. Reinvesting in Research and Development, and bringing smart, young engineers into the fold to tell the old-timers things they didn’t necessarily want to hear about innovation and use of new materials — not to mention a clever use of its abundant suppliers in a nearby five-state area — has kept the company one step ahead of the game.
And while we are on the subject of games, the fixed-seating projects that account for about 30 to 40 percent of American Seating profits are subject to the same type of rigorous R&D as transportation seating.
“I can pretty much guarantee your butt’s been in one of our seats, somewhere,” said Nelson W. Wilfore, the company’s director of contracting. Wilfore seemed in a jovial mood this day, just having secured the contract to replace the seating at the Miami Dolphins football stadium. NFL representatives have been encouraging the Dolphins’ owners to spruce up its aging facility in hopes of hosting future Super Bowls in the fun and sun of South Florida.
American Seating not only manufactures and installs seats for football stadiums, but outfits a majority of Major League Baseball venues, college stadiums, and arenas, performing arts centers, and university lecture halls and classrooms.
Among the football facilities with American Seating seats in them are the New York Giants/New York Jets MetLife Meadowlands Stadium (home of last year’s Super Bowl), the Baltimore Ravens M&T Bank Stadium, Cleveland Browns Stadium, The University of Michigan “Big House,” Ohio Stadium at Ohio State University, and the University of Nebraska Memorial Stadium.
There will be no American Seating manufactured seats at this Sunday’s Super Bowl Game. The contract for the University of Phoenix Stadium in Glendale, Arizona went to another seating company.
In Major League Baseball, three of American Seating’s earliest projects were Boston’s Fenway Park, Detroit’s original Navin Field, and Chicago’s Wrigley Field.
“We’re very much akin to what is going on in this world,” Wilfore said. “We did the original seats at Fenway Park in 1912 and redid them. That was a great project. That had more historic value than any other project we have gone through, and so there were a lot of rules that we were faced with in supplying that we never saw on any other project.
“We actually took iron out of their seats that were built with very, very old iron. And we either re-used the iron or we built iron to exactly match it so that when you went back to look at it, it looked exactly the same. Which included planks because a lot of the seats, if you’ve ever been there, are actually bleacher-type seats. They’re wood, so we purchased the wood so that when we put it in there it would give it that look of the old seats.
“There was a lot of reuse of materials that went into that and also very heavy monitoring of what left the yard and what came back in. They were very careful about that, and I’m not sure what the percentage is but I know that at least 50 percent of the facility is original. It’s just stuff we took out and put back in after it was cleaned up.”
Today, American Seating is responsible for the rows and rows of seats at the St. Louis Cardinals Busch Stadium, Milwaukee Brewers Miller Park, Detroit Tigers Comerica Park, Dodger Stadium, Miami Marlins Park, PNC Park in Pittsburgh, Camden Yards in Baltimore, and Nationals Park in Washington. DC, along with Fenway and Wrigley.
Some of the arenas its seats can be found include Brooklyn’s Barclay Center, the Verizon Center in Washington, DC, Pauley Pavilion at UCLA, and the Dean Dome at the University of North Carolina.
We did the original seats at Fenway Park in 1912 and redid them. That was a great project. That had more historic value than any other project we have gone through. Nelson W. Wilfore, American Seating Company
Such a wide variety of products covering all corners of the country is a testament to the talents of the Grand Rapids-based workforce of approximately 450 UAW members.
More than 75 percent of the nation’s city-service bus seats are made by American Seating. American Seating purchases 75 percent of its raw materials from Michigan, Ohio, and Indiana and almost all raw materials used by American Seating are sourced domestically.
The 450 UAW workers in Grand Rapids are proud to work for a Made in America manufacturer and further relish the input allowed between management and those working the factory floors.
“I think we do a lot of things here in a different sense at the way we look at things,” said Kurt Hillary, vice president of operations. “Managers are in charge of running the company and making sure things are happening the right way. But it doesn’t mean I consider, in my office of VP of Operations, that I know how to fix this line. Gull, who works on this line, Gabe, Brad and the engineer that helps out, they know how to fix this line. So what I am charged with to make it run right is give them the opportunity, give them the space, give them the authority and the tools so they can actually do this. Then we sit in a meeting at the end of every day and they say, ‘Kurt we need this and we need that.’ I can say, OK, let’s do it.”
Brad Wilson has been working on the factory floor at American Seating for 35 years. He appreciates the camaraderie between management and his UAW brothers and sisters.
“We can run overtime if we have heavy, special orders,” he said. “We run two shifts in this plant and sometimes a skeleton of two shifts at the other plant. We’re here to get the job done and get the stuff out the door.
“You’re always going to run into problems with management at times but we’re able to sit down as a team and work out the best way to solve a problem.”
A lot of history has passed since American Seating began as a school desk and chair assembly. It’s American-made and has stayed that way. Presidents have adorned its seats. Famous athletes and musicians have savored the supports. So many extraordinary things have taken place upon an American Seating seat it would be impossible to count them all.
In 1942 American Seating produced more than 5 million chairs for the military during World War II. Its Grand Rapids plants were used to produce aircraft wings for American fighter planes.
Seventy years later, in February 2012, Vice President Joe Biden visited American Seating to discuss the Obama administration’s plan to help businesses bring manufacturing jobs back to America.
“American Seating’s mission is to make seats and other furniture for everyday people, for just about every public setting imaginable,” said American Seating President Tom Bush. “We’re pretty proud that we’ve been doing that for more than 125 years, right here in the same location, right here with a Grand Rapids, Michigan, Made in America workforce.
“American companies need Washington to focus on how important it is for our country to continue to manufacture products right here. With the right environment and a level playing field, there is no reason why we can’t grow our manufacturing base.”