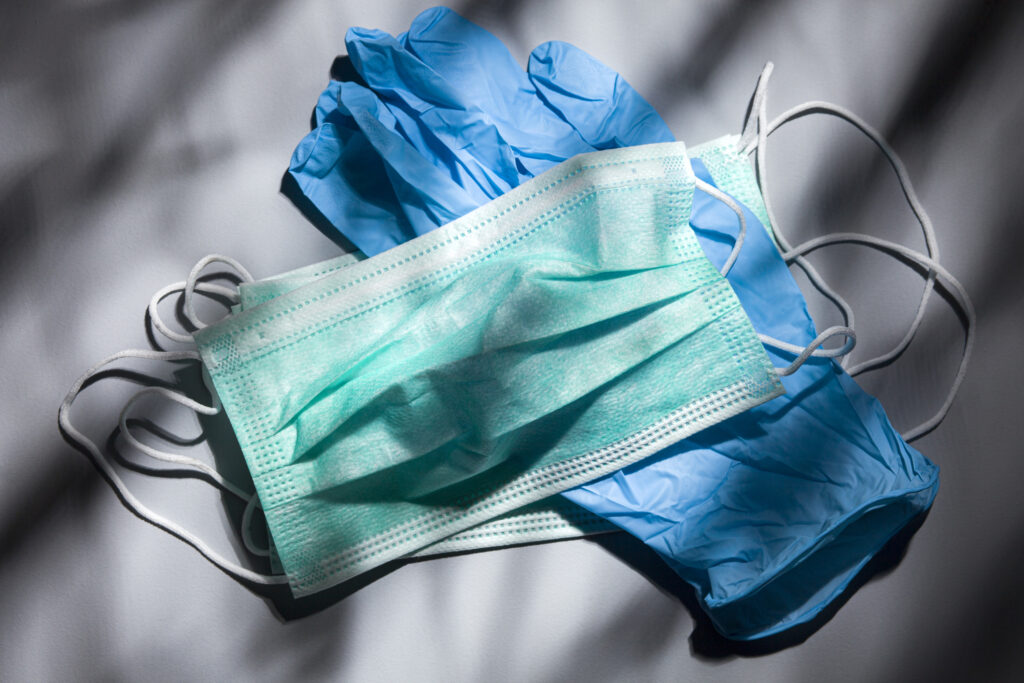
Experts tell a Senate panel that America’s continued reliance on China is one of the reasons why shortages of personal protective equipment remain.
Neil Gilman comes from a long line of American manufacturers.
His ancestors built one of the first textile mills in Connecticut. In 1929, his father built a company that pioneered the development of football training equipment.
Gilman now runs Gilman Gear, which makes a range of products for a variety of sports and is the country’s leading maker of blocking and tackling dummies and sleds. But when the COVID-19 pandemic struck the United States earlier this year, Gilman found his business collapse overnight, as sports teams from the youth level to the pros canceled or postponed their seasons.
That’s when Gilman decided to pivot from football to the frontlines. Hospitals couldn’t get the personal protective equipment (PPE) they needed because the supply chain from China had been depleted, and Gilman decided to help.
“Gilman Gear had a large cut and sew operation,” Gilman testified a Senate panel on Tuesday. “I was determined to make isolation gowns because we had the equipment to cut and sew them. I quickly got a sample from a local hospital. Designed my own pattern. Researched the materials the gowns are made of and built a prototype using a non-woven polypropylene material. I sent it over to Yale New Haven Hospital. They evaluated it and awarded me my first big order. I was able to get business because there was ‘surge demand.’”
Gilman’s efforts bridged the gap during a critical time, but problems soon arose. Hospitals needed the gowns fast – and cheap. Gilman invested in new machinery and managed to up his output from 200 gowns a week to more than 12,000 gowns a week, he recalled.
But the hospitals didn’t want to pay more than they were used to paying for gowns from China. And Gilman, who faces higher labor and material costs as an American manufacturer, can’t compete on cost, especially considering that China’s regime is heavily subsidizing its own PPE industry.
“My American-made gown is two to three times more expensive then those made in China. However, my American-made gown is a higher quality and meets a higher level of protection,” Gilman told the Senators. “But in the PPE market, an isolation gown is considered a commodity item and buyers in the medical community are just looking for the cheapest price.”
As the United States faces a new wave of COVID-19 cases, the country also continues to face dangerous shortages of PPE and other critical equipment needed by health care workers and others on the frontlines of the virus.
Part of this, of course, is due to a lack of domestic manufacturing of both PPE and products needed in the critical supply chain, coupled with a mass shortage of PPE globally. The Trump administration also failed to respond quickly and coordinate efforts, which has complicated things.
But in the months since the pandemic struck, countless American manufacturers like Gilman Gear switched their production lines to make everything from face masks and gowns to respirators and ventilators. Why are there still shortages?
The U.S. Senate Committee on Commerce, Science & Transportation set out to find out why on Tuesday, holding a hearing titled “Examining the American Manufacturing Industry’s Response to the COVID-19 Pandemic.”
Along with offering thoughts on why the United States is at this point, panelists provided expertise on what needs to happen to improve America’s domestic manufacturing and critical supply chain.
Among those presenting testimony alongside Gilman were Ravi Bulusu, founder of MolMas; Rick Krska, president and chief executive servant of InkCycle, Inc,; Tiffany Stovall, chief executive officer of Kansas Manufacturing Solutions; and Michael Wessel, a commissioner on the U.S.-China Economic and Security Review Commission.
The biggest talking point among the speakers: China.
When it comes to PPE, China dominates in manufacturing. It goes without saying that the United States has heavily relied on China for PPE, including everything from face masks and gloves to medicine (80 percent of APIs are imported from overseas, with a large portion coming from China) to even cleaning supplies.
But it’s even more than that. Wessel noted that while the focus of Tuesday’s hearing was on PPE and other medical equipment, America’s reliance on China for its manufacturing has been detrimental to the U.S. economy and national security as a whole (not to mention millions of lost jobs). The Chinese Communist Party (CCP) is using our dependence on Chinese manufacturing to advance their agenda to dominate globally by 2025, he said.
“As predatory pricing drives outsourcing of jobs and offshoring production, it can lead to a severe loss of domestic productive capacity. Industry after industry has faced this problem,” Wessel testified. “Steel, aluminum, solar cells, rare earths have gotten the bulk of the attention. But China’s industrial policies, as well as our own short-sightedness, have also created an unacceptable and dangerous reliance on China for our pharmaceuticals, active ingredients which are also known as APIs, medical devices, and equipment, including PPE.”
China’s dominance often appears even when manufacturers are working hard to make and source their products in the United States.
Take IncCycle, Inc., which is run by Rick Krska. The company remanufacturers inkjet cartridges, and has been determined to maintain as much U.S. manufacturing presence as possible, he told the Senate panel.
However, the company found that to stay afloat, it needed to import some of its products from China. Earlier this year, Krska and some of his colleagues were returning from a sourcing trip in – wait for it – Wuhan.
They quickly realized how serious the pandemic would become. “This inspired us to begin exploring how we might serve and do a business pivot into manufacturing PPE supplies. Quickly we found that most of the PPE products came from China. Very few U.S.-produced products were available,” Krska said.
The company first created a hand sanitizer, which could be bottled in their home town of Kansas City. But the company still had to buy materials from China, because the U.S. didn’t have any small bottle manufacturing capabilities.
“Interestingly, the strange Chinese ‘economics’ we had seen in our core business was to be found in Chinese bottle manufacturing industry as well. Forced to buy bottles in China, we were purchasing our labels from a local Kansas label manufacturer at around $0.15,” Krska recalled. “The Chinese bottle supplier offered to print and apply the labels for a single cent. The cost to print a label in the U.S. – 15 cents. The cost to print the same label AND apply it to the bottle in China – 1 cent. The U.S. loses label printing jobs and manufacturing application jobs.”
American manufacturers want to make and produce their products in the United States, Krska said. But unless the United States gets serious about strengthening its domestic production capacity, China will continue to dominate.
“It has been our experience and observation that manufacturing companies in China are strongly supported by their government. It is my belief that if [we] seriously desire to bring manufacturing and critical supply chains back to the U.S., it will require strong support from Washington,” he testified.
Gilman echoed those remarks, telling panelists that policies like implementing a Buy American preference across all federal agencies that purchase PPE are among those that will help manufacturers like him continue their efforts to address the ongoing crisis.
“What we want, to use a football term, is a level playing field, so we can compete with China,” he said. “What’s at stake here, is the future of manufacturing PPE in the state of Connecticut and for that matter, across the United States. If we let China dominate the market for PPE, if we let them control the supply chain for PPE, doesn’t that compromise our ability to cope with this pandemic? Do we want to be at the mercy of China, when and if there is a pandemic in the future?”