Meet six of the 3.2 million Americans who lost their job due to trade with China.
Wanda Perdue was a sprightly 24-year-old woman when she walked into the Stanley Furniture plant in Martinsville, Va. to begin her first day on the job in 1973.
In October 2010, she walked out of the Stanley Furniture factory for the last time after her shift and just kept moving forward, unable to summon the courage to turn around for a final peek.
“The day I left, I didn’t look back,” she said. “When I left I went out the door, right to my car and never looked back. It’s sad, too, isn’t it?”
After 37 years of working on the production line making drawers and doors, Perdue became another victim of outsourcing — or what former presidential candidate Ross Perot, referring to the North America Free Trade Agreement (NAFTA), called “a giant sucking sound.”
Perdue’s job was sent to China. She’s not alone.
Millions of Americans have lost their jobs because of unfair trade with China. A new report from the Economic Policy Institute finds that 3.2 million Americans have had their job outsourced to China since 2001. That number is up from 2012, when EPI found the growing trade deficit with China cost more than 2.7 million jobs from 2001 to 2011.
And while the United States has gained back the number of jobs lost in the Great Recession, most of those jobs are low paying, often in the service industry. Manufacturing job growth continues to drag. President Obama set a goal of creating 1 million new manufacturing jobs in his second term but only 257,000 have been generated thus far.
Americans living in small, rural factory towns continued to be devastated by lack of work.
“They made the arrangements to send the jobs to China and elsewhere because they were making more money that way. They didn't have to tell us (the jobs were being offshored), we figured it out. When you see strangers coming in your workplace and all this, you know what's going on." —Wanda Perdue
One of the hardest hit areas is Martinsville. The Southside Virginia city once was a major textile center known as the “sweatshirt capital of the world.” It also served as a manufacturing hub of furniture. Now it has seen nearly all of its manufacturing operations shut down, resurfacing in China, Southeast Asia, or Mexico.
In 2010, Martinsville had an unemployment rate of 22 percent. Today it hovers around 15 percent, far above the national rate of 5.8 percent.
Baby Boomers have been hardest hit. Getting good manufacturing jobs right out of high school or community college, they planned a lifelong career, often at one job, expecting health benefits and pensions upon retirement. Many were following the model careers of their parents who were able to live a comfortable middle-class life and retire with a safety net.
“They made the arrangements to send the jobs to China and elsewhere because they were making more money that way,” said Perdue. “They didn't have to tell us (the jobs were being offshored), we figured it out. When you see strangers coming in your workplace and all this, you know what's going on. When I first went down there, it was a good place to work.
“China furniture doesn’t last long and I think that's the intention of the whole thing. It's not quality work, like what we did. They know people are going to be looking for furniture and even though they buy new furniture, they'll probably be out looking for something else in another year or so.”
Despite her 37 years on the job, Perdue was let go without severance or benefits. She used her 401k funds to get by while taking care of her husband who has suffered from heart problems for several years.
Most of the Stanley Furniture jobs ended up in China, although the company tried to keep some work in the United States at its plant in Robbinsville, N.C. The Robbinsville plant was shut down earlier this year, with 400 workers displaced. Stanley Furniture had previously closed its facility in Stanleytown costing 530 jobs. Stanley has basically ended the production of its furniture in the United States.
Perdue secured a part-time job at Walmart before her final shift at Stanley Furniture. Through the Trade Adjustment Assistance Act (TAA), she received funding to go to Patrick Henry Community College to study for a career as an office administrator. The TAA allows workers who have lost their jobs because of a trade-related reason to go for free retraining while still collecting unemployment benefits.
But after finishing school, Perdue had no luck finding a local office job. She settled in at Walmart.
While it’s not the job she hoped to get, it assures her the health insurance she badly needs for her husband and herself.
“I'm 61 years old, but if I was 16 like my granddaughter and know what I know now, I would have done things different like get an education,” she said. “But I had a career at Stanley, and I didn't think I needed to go nowhere.”
Tom Gaulrapp is another American manufacturing worker who didn’t think he needed to go anywhere. He spent 33 years operating multi-million dollar, high-tech equipment at the Sensata Technologies facility in Freeport, Ill. before the automotive parts plant ceased operations at the end of 2012.
Most of Gaulrapp’s tenure was with the Honeywell Corporation auto sensor division. In October of 2010, Honeywell sold this division to Sensata, which was owned by Bain Capital — the company made famous during the 2012 election since presidential candidate Mitt Romney once served as its CEO.

Bain Capital disassembled the plant’s interior piece by piece and sent the equipment to China, where workers were paid 99 cents per hour, according to a report by the Institute for Global Labour and Human Rights.
The move to offshore baffled workers. Sensata Technologies amassed record profits from the auto sensor business in 2010 and 2011. There also was rich history in Freeport, where its products were researched and invented in the 1960s by two local engineers who drove to Detroit to pitch their ideas to American auto manufacturers.
So why was this profitable plant being shut down?
“The Chinese government provided them with a plant, provided them with 99 cents an hour labor and they wanted the money,” Gaulrapp said. “When is enough, enough? Where is any kind of sense and responsibility back to the communities? They are using our infrastructure and then they just pack up and leave?
“I don’t have anything against the Chinese workers at all, I feel sorry for them. It bothered me that a company that set records for profitability when it was in Freeport would pick these jobs up and move them over there just for greed. You would hate to see if it was a situation where they either had to do that or go out of business. But that was not the situation here.”
Gaulrapp and the other 170 laid-off Sensata workers endured insult to injury when Chinese technicians came to Freeport to learn the operation while the Sensata employees trained them. Then, machines were disassembled and sent to China while Sensata’s American workers watched in disbelief.
“The Chinese technicians were supposed to be trained by us so that they could go back to China and train the Chinese factory workers,” Gaulrapp said. “It was ridiculous because they weren’t even paying attention. One guy made a comment that when they got the stuff back to China the first thing they were going to do is tear off all the safety equipment.”
At 56 years old, Gaulrapp will soon complete the coursework required to earn an associate degree in accounting. He was able to go to Freeport’s Highland Community College through the TAA program just as Perdue had done in Martinsville.
And like Martinsville, the city of Freeport is reeling from the numerous manufacturing plants that have closed during the past 15 years. Honeywell, which sold its auto parts division to Sensata and ultimately Bain Capital, once employed thousands of people in the area. It is now down to a workforce of several hundred.
“It was the best job in town, a good-paying manufacturing job,” Gaulrapp recalled. “You didn’t get rich off it, but you were able to make ends meet. It was a middle-class job. There’s not going to be a middle class anymore. There’s going to be rich people and poor people and that’s going to be it.
“The problem is when you lose jobs like we had, these well-paying manufacturing jobs, it brings the wage base down in the entire community.”
The people of Martinsville, like Perdue, certainly know about lower wages and loss of jobs.
Mary Moyer-Redd is another Martinsville worker who planned on retiring from her longtime job. She worked in the Information Technology department of Tultex Corporation, one of the world’s leading textile mills producing fleeced sportswear and sports apparel.
Tultex, through many acquisitions in the textile industry, had employed more than 8,000 people in 1984. But because of foreign competition with inexpensive labor, business began to decline by the late 1990s. Tultex filed for Chapter 11 bankruptcy protection in December 1999. It was reborn as a division of TSC Apparel based in China.
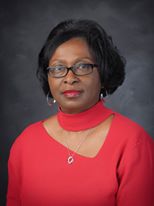
Moyer-Redd had worked 20 years for Tultex when she arrived at work one day only to learn it would be her last.
“They had a group of us in on December 3, 1999. There were a lot of IT people,” she said. “They told us that we were being laid off, we had to gather our stuff up and exit the building.”
Moyer-Redd planned on working toward her retirement with Tultex when the textile rug was pulled right from under her.
“I had been employed there for 20 years and of course I had vacation, holidays, 401k, dental, medical. I was looking to retire from that company,” she said.
But Moyer-Redd is not bitter or complacent. She was born and raised in Martinsville and still lives in the city.
“It was really a great company to work for,” she reflects. “Martinsville got hit really, really hard and it’s been a struggle, from God be to glory. You know, everything happens for a reason. I thank God for the positions that I do have now because a lot of people have not bounced back and do not have anything.”
Moyer-Redd now works three days per week at the Henry County J & D Court and two days at the New College Institute in Martinsville, where young workers are trained for future employment in the area’s changing business landscape.
“There are no jobs here. That’s why a lot of our kids go off to school but they don’t come back home. They don’t have anything to come back home to.” —Frances Kissee
There is a long list of companies in Martinsville and Henry County that shut down in quick succession. Previously, if a factory closed, you could find another job sewing at a mill or in the furniture industry.
DuPont had one of the world’s largest nylon manufacturing factories in Martinsville. The plant covered about 550 acres and employed 4,600 workers in the 1960s. DuPont closed its facility in 1998 resulting in the loss of its last 400 jobs.
And as DuPont went, others followed: Tultex, Stanley Furniture, Pluma Fleece, Ashmore Sportswear, Bassett-Walker Apparel, Fieldcrest Cannon towels, and the old Panill Knitting Company, which was bought out by Sara Lee Apparel then ultimately shut down under the Hanesbrands name.
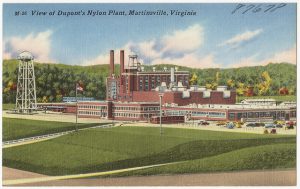
Martinsville resident Frances Kissee has really shown her mettle in her quest to stay in the ghost-town like atmosphere of the once thriving manufacturing city. The 57-year-old experienced seamstress has lost six jobs to closures during the past 18 years.
“My first job was at Sara Lee which they later called Hanesbrands,” Kissee said. “I worked there about 17 years. I was a seamstress and I also was in quality control, so I would go around to the different departments and check their work.”
The Sara Lee factory made fleece wear, sweatshirts, and sweatpants, contributing to Martinsville's “sweatshirt capital of the world” designation. The Sara Lee sewing factory closed in 1996.
“When the factory closed, I guess we didn't realize we had it made with that company,” said Kissee. “I got laid off before the plant actually closed but once I got laid off it wasn't long after that the plant shut down.
“At first, when the plant said they were closing down, they denied the fact they were sending the jobs overseas, so we did not get approved for ‘Trade Act’ until almost a year later. When I came out of work in 2011, I went ahead and signed up for school so by the time they got Trade Act approved, I only had a few months left to finish school.”
Kissee received an associate degree as a paralegal but there were not any job openings in the Martinsville area. So with her fierce determination, she returned to school and got another associate degree in Early Childhood Education.
“Working with children, I could either open a day-care center or go into the school system. I am thinking about going back and getting my bachelor's degree,” she said.
Kissee says there was a bit of an uproar in Martinsville after word got out that Hanesbrands had moved its production to China and Vietnam. But it didn’t bother her too much, because she knew there was always another factory down the road.
She finally came to the realization that she wouldn’t retire from a Martinsville factory as both of her parents had done.
“There are no jobs here. That’s why a lot of our kids go off to school but they don’t come back home,” she said. "They don’t have anything to come back home to.”
Among the small number of fortunate laid-off workers that had a job to come back to are the employees at the U.S. Steel Tubular Operations in Fairfield, Ala. The plant was idle for a short time in 2009 when manufacturing orders dropped because of China’s illegal dumping of its steel into the U.S. market.
The plant’s employees were laid-off at various intervals but were lucky to be called back after the U.S. Commerce Department and the International Trade Commission ruled that China was guilty of flooding the American market with below-cost, subsidized steel. Without this ruling, which carried financial penalties for China, the steelworkers may not have been called back. Levying the duties on China helped put American steel companies back on a level playing field with China so they could be competitive in the global marketplace.
Valerie Lambert has worked at the Fairfield Tubular Operations for 15 years and was part of those layoffs in 2009. She has graduated from a grinder on the mill floor to working with all of the safety documents at the pipe-making facility. She also leads the local “Women of Steel” program.
“I wasn’t really sure we would be back during those layoffs,” Lambert said. “When you go to the store and see everything is made in China, you start to wonder if your job is going to be gone because of China.”
Fortunately Lambert was called back after a five-month layoff. But she lives with the constant reminder that one day she could face another lay-off, perhaps permanent, if steel dumping in America once again slows down production at U.S. Steel facilities. During a recent trade case against South Korea and its illegal dumping, U.S. Steel plants in McKeesport, Pa. and Belleville, Texas idled and have not returned to production, leading to 260 employees being laid off.
“It’s always there, the possibility of losing our jobs because of the foreign steel,” Lambert said. “It’s always a possibility. I’m hoping the quality of our product will separate us and we will continue to have our jobs for a long time.”
Lambert’s co-worker Shawn Winholtz has worked at the Fairfield Tubular Operations for 10 years. Having worked at small welding shops before getting hired at U.S. Steel as a thread machine operator in the pipe division, Winholtz sees an opportunity to make a career of his work. But after being laid off for five or six months in 2009, he knows there are no guarantees.
“The steel market should be closed to outside competitors. Our trade is not fair. There’s a lot more coming in to this country than is going out,’’ Winholtz said. “The fact that we could lose our jobs at any time stays in the back of your mind. It’s always a threat. But I don’t lose any sleep over it.”
But a lot of workers suffer insomnia and anxiety while waiting to find a meaningful job in communities that are losing opportunities.
The workers at U.S. Steel were fortunate to be able to return to their jobs after layoffs. U.S. Steel is not going to move its operations to China and displace all of its workers. Steelworker jobs are threatened indirectly by Chinese imports into the United States.
The workers at most American manufacturing facilities are not so fortunate. They lose their jobs as a result of a direct connection to China. Whole businesses are sold and shipped to China, where product manufacturing is now in the hands of Chinese workers.
Just ask the workers of Martinsville and Freeport, two of hundreds of American cities devastated by the continuing offshoring of the American workforce.
“It’s all about the money,” Gaulrapp said. “When a profitable company decides to move to China, it just shows you how little they care about the livelihood of the workers of America.”