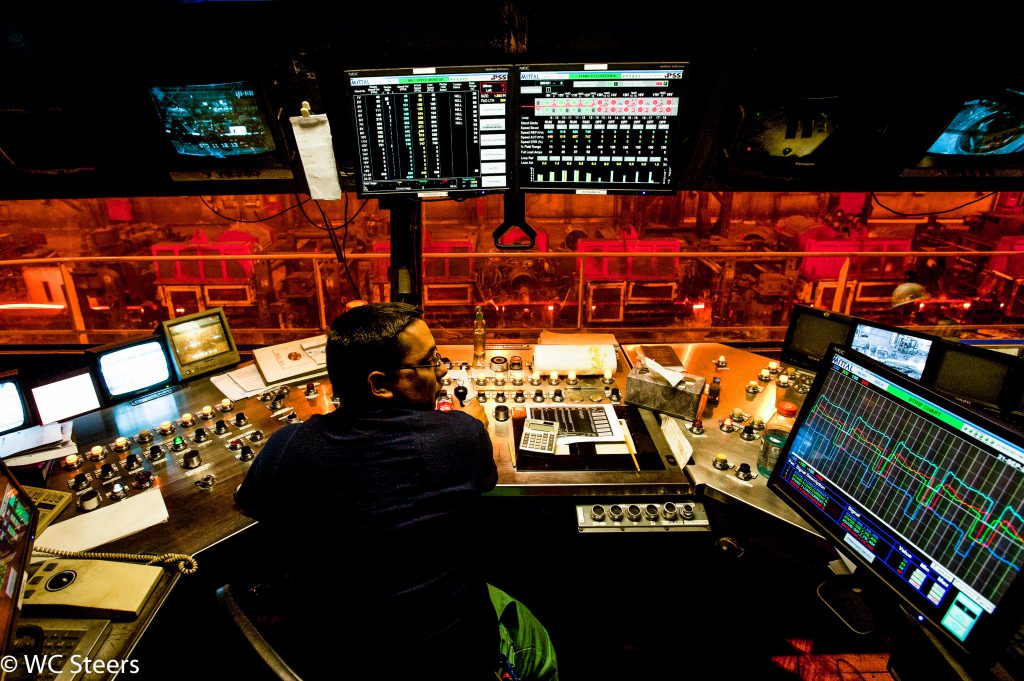
“It’s not your grandfather’s factory anymore,” say program leaders.
Anan Ayyad is a 21-year-old college student and a full-time employee at ArcelorMittal’s Burns Harbor, Indiana steel mill located at the tip of Lake Michigan. Many college students earn advanced degrees in various fields of interest before they decide a suitable career choice.
Carrying such a heavy load as student and full-time steel mill worker set him apart from his fellow higher education seekers. Ayyad had an inkling about his future career early on and he has made the most of the opportunities that have presented themselves to such a young man. Some students wait until they are 30 or 35 years old before they can confidently say what they want to do with their lives.
“My main interest since high school had actually been engineering generally, and my main interest in engineering was actually about electrical or mechanical,” he said. Shortly after graduating high school, Ayyad enrolled at Moraine Valley Community College near Chicago and joined the electronics program. In February of 2014 he discovered that ArcelorMittal, the top producer of steel and mining in the world, was affiliated with his school, offering entry into its Steelworker for the Future program.
Two months later, Ayyad had his first interview and test to seek qualification for ArcelorMittal’s unique training program.
“I’ve been in the program with ArcelorMittal at Burns Harbor as an intern since June 9, 2014. My internship went for eight weeks continuously, and I was offered a second internship with the company as well,” said Ayyad. “During the second day of my second internship at ArcelorMittal, I passed my exam that is required by the company for you to qualify and become a maintenance technician.”
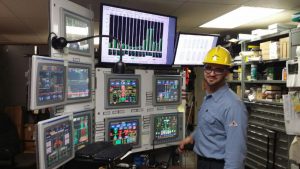
Ayyad is currently attending two schools – the ArceloMittal training school and, having earned his associate’s degree at Moraine Valley, he is now at Purdue University-Calumet in pursuit of a Bachelor of Science degree. He is thinking about the future and the career advancements he could make with his advanced education.
But to complete the Steelworker for the Future requirements, he needed only to earn his associate’s degree.
Hitting the Books
America has lost nearly 5 million manufacturing jobs since 2001. A lot of that is due to offshoring; companies have literally moved their operations to foreign countries like China, Japan, and Mexico to take advantage of low wages, taxes, lack of employee safety regulations, or mercantile practices like currency manipulation. These companies are often subsidized by foreign governments, creating a playing field on which American manufacturers cannot compete. China is the foremost offender, taking whole factories or products and selling them back into the American market at a point often far lower than a true market price. Making low-quality and highly subsidized steel is one of China’s most foremost examples.
R.D. Parpart is the team leader for ArcelorMittal’s Steelworker for the Future program. He recognizes the un-level playing field that American manufacturers face each day. But with constantly changing technologies, he and ArcelorMittal executives were quick to see the need of replacing near-retiring workers with a new generation of tech-savvy job seekers who were not quick to embrace employment in a stifling, dirty factory. Parpart likes to point out that “it’s not your grandfather’s factory anymore.”
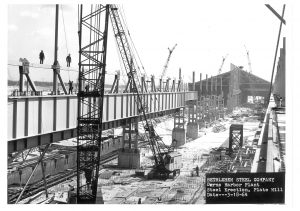
When American unemployment claims hovered in double digits, companies complained about unfair trade practices and a lack of skilled workers. Unemployment claims have since dropped to 5.5 percent, but manufacturers still report that it’s difficult to hire workers with 21st century skills. Luckily, there are hundreds, if not thousands, of job training programs available to learn the necessary skills of manufacturing today. Companies, unions, high schools, trade schools, and community colleges are all a part of this equation. President Obama has been continuously traveling the country promoting manufacturing hubs that combine private businesses, executives, academics and community colleges. And with the president comes government financial aid that encourages businesses to invest as well.
“We require a skill base now that wasn’t required 30, 40, 50 years ago so with today’s automation, students or prospective employees have to have a much stronger skill base in science, automation, math, and engineering-type skills,” said Parpart, a long-ago internship graduate. “So we created this program – Steelworker for the Future – and we partner with local community colleges that are close to our facilities and the students can go to one of the specific schools and enroll in a specific curriculum.”
The ArcelorMittal Steelworker for the Future team has worked with these community colleges, helping them build the best-suited curriculum for the more recent changes in automation and technology used in mixing, melting, and pouring steel. To qualify, a student must maintain a 2.8 GPA and pass a drug screening in the first semester of core classes. If successful, students can then apply for a paid internship.
Students continue schooling into their second semester and are brought in for other hiring qualifications, interviews, additional drug screening, and some assessment testing.
We require a skill base now that wasn’t required 30, 40, 50 years ago. R.D. Parpart, Steelworker for the Future team leader
If all goes according to plan after two complete semesters, students are then eligible to become interns. They then take the first of two eight-week, paid internships. After that first internship, steelworker students go back to the college to study for a third semester. After completion of a third semester, they would begin their second internship and eventually return to school for their fourth and final semester.
“As a full-time student, after that fourth semester they would earn their associates degree,” said Parpart. “Then at that point, they will have done two internships, they will be tested with our craft entrance exam, and assuming they pass all other hiring requirements, they’ll be extended an offer for full-time maintenance technician trainee.”
Times have changed, and it’s simply not as easy as walking up to the mill’s gates announcing you are looking for a job. These days a steel job at ArcelorMittal seems to require giving part of your life along with the blood, sweat and tears of hard work and long hours for the title of maintenance technician.
But the important word in your title is technician. Don’t associate maintenance with janitor, a job that finds you cleaning up after everyone’s mess. It’s the technical skills that keep the mill operating at optimum performance.
“By the third year of full-time employment is when all the hard work pays off,” said Parpart. “The first year you are going to spend in continued training, the second year is when you start to fit into you own department, so by the third year, the average maintenance technician makes $90,000 per year. That does include some overtime and our standard incentive plan and the shift differential and stuff like that, but the average steelworker at ArcelorMittal makes $90,000.
“You can be 23 years old and making that kind of money in a high-demand field. That’s real good.”
Everywhere ArcelorMittal is
The Steelworker for the Future program began, ironically enough, in 2008 and a time of recession. “(It began) during a very rough time, and I like to talk about this because we were committed to the program because we knew long-term this need is going to continue,” said Parpart. “Regardless of the economy, and in good times and bad times, we’re still going to need skilled employees to continue to keep our mills up to date and operating. So even through times of recession we continued our program.”
ArcelorMittal has partnered with 10 colleges in five states. The colleges are located practically in the backyards of its plant, with the most heavily concentration being in the Northwest Indiana and suburban Chicago areas. They include Indiana’s Ivy Tech Community College campuses in Valparaiso, East Chicago, and Gary; and Moraine Valley Community College in Palos Hills where Ayyad earned his associate’s degree, and Prairie State College in Chicago Heights – both in Illinois. Another top steel-producing area for ArcelorMittal is near Cleveland. As such, the program is also available at Cuyahoga Community College in Cleveland, Lakeland Community College in Kirtland, and Lorain County Community College in Elyria. In Pennsylvania the Steelworker for the Future program is in partnership with Delaware County Community College in Media and at Penn State campuses in York and Harrisburg. The final partnership program is at West Virginia Northern Community College in Weirton.
“Right now, there are 190 students in the related curriculum with the partner colleges who met the criteria and are at some stage of an internship or pursuing graduation,” said Parpart. “Of the students that graduate and pass our hiring requirements, 93 percent of them have accepted our offer of full-time employment.”
As for Ayyad, he knows he is fortunate getting through the Steelworker for the Future program and the many benefits it brings. He is proud to be an ArcelorMittal maintenance technician electrical (MTE) and a member of the United Steelworkers union. But he already has ideas about continuing education and changing technologies.
“I wouldn’t say I was surprised, going to ArelorMittal, but I was definitely impressed,” said Ayyad. “These days as a college grad, after you have had your associate’s degree and you go out into the field you’ll be expecting a pay grade from $30,000 to $40,000. And if you are an intern you know you are lucky to make $12,000 to $14,000 per year. I was actually pretty impressed that ArcelorMittal offered what it did offer and was pretty much a fine program.
I wouldn’t say I was surprised, going to ArelorMittal, but I was definitely impressed. Anan Ayyad, Steelworker for the Future graduate
“The money is quite fine, but I can see myself utilizing my degrees or knowledge. The one big part is that I could successfully help engineer or design or make manufacturing plants more efficient and eco-friendly. That is the direction I hope to be going into. I would love to one day be on a committee that had the power to make our production more efficient, and us being able to compete with more of the offshore (product) and get some of our stolen business back.”
Parpart, meanwhile, has extended his outreach program to high schools and middle schools located close to the ArcelorMittal plants. He and his team spoke to nearly 20,000 younger students in 2014.
“One of the main parts of our outreach program is getting out there and taking to students about manufacturing and skills in general,” he said. “It’s not about getting a college degree, it’s about getting skills.”
ArcelorMittal is the world’s leading steel producer and mining concern with 222,000 employees operations in 19 countries. With global headquarters in Luxemburg and American headquarters in Chicago, this behemoth of a company still only produces about 6 percent of the world’s steel.
Said Mary Beth Holdford, the company’s Division Manager of External Communications: “At the end of the day we are a global company but we employ more than 20,000 Americans here in the U.S., we make steel here in the U.S. from raw materials to finished products, and we invest in our communities. We are a global company but we also like to think of ourselves as an American Company in so many ways.”
Learn more about the Steelworker for the Future program here.